Ремонт
и проверка автосцепного устройства
подвижного состава производятся в
контрольных пунктах автосцепки (КПА)
депо и отделениях по ремонту автосцепки
вагоно- и локомотиворемонтных заводов,
имеющих специальные удостоверения
установленной формы, выдаваемые
Департаментом вагонного хозяйства (ЦВ)
МПС России.
Размещение
технологической оснастки в пунктах
ремонта автосцепного устройства должно
обеспечивать выполнение требований
настоящей Инструкции, а также техники
безопасности и промышленной санитарии.
Контрольные
пункты автосцепки депо и отделения
ремонтных заводов должны иметь необходимую
технологическую оснастку, два комплекта
проверочных и один комплект контрольных
шаблонов в соответствии с приложениями
1 и 2 настоящей Инструкции. Шаблоны должны
соответствовать действующим техническим
требованиям, утвержденным ЦВ МПС. Шаблоны
проверяются на ремонтных предприятиях
не реже одного раза в год с постановкой
даты проверки согласно Методическим
указаниям контроля СДК для автосцепных
устройств вагонов РД 32 ЦВ-ЦЛ 027—91.
При
полном осмотре съемные узлы и детали
автосцепного устройства снимают с
подвижного состава независимо от их и
направляют в КПА или отделение по ремонту
автосцепки завода для проверки и ремонта
в соответствии с требованиями, изложенными
в главе 2 настоящей Инструкции. К несъемным
деталям автосцепного устройства
относятся: ударная розетка, передние и
задние упоры, располагающиеся на
хребтовой балке, детали расцепного
привода (фиксирующий кронштейн, кронштейн
и расцепной рычаг). Ремонт и проверку
несъемных деталей производят на подвижном
составе, за исключением случаев, требующих
их демонтажа.
Детали
автосцепного устройства, снятые с
подвижного состава и подлежащие проверке
и ремонту, должны быть очищены от грязи
средствами, имеющимися в распоряжении
пункта ремонта. После очистки корпус
автосцепки, тяговый хомут, клин (валик)
тягового хомута, маятниковые подвески
центрирующего прибора, болты паровозной
розетки должны быть подвергнуты
неразрушающему контролю. Стяжной болт
поглощающего аппарата, опорную пластину
поглощающих аппаратов ПМК-110А и ПМК-110К-23
подвергают неразрушающему контролю
только после их ремонта сваркой.
2.4 Разборка механизма автосцепки са-3
Разборка
механизма автосцепки СА-3 осуществляется
в следующей последовательности:
разъединяют цепь расцепного привода,
освобождают расцепной механизм, затем
вытаскивают запорный болт. Вытаскивают
валик подъемника через отверстие в
стенке корпуса, вытаскивают из корпуса
замок с предохранителем. Затем снимают
с полочки и извлекают замкодержатель.
Далее с опоры стенки корпуса снимают
подъемник.
При
деповском ремонте вагона разборке
подлежат только неисправные поглощающие
аппараты, при капитальном ремонте все
аппараты должны быть разобраны.
2.5 Ремонт автосцепки са-3
Изгибы
хвостовика корпуса автосцепки и уширение
зева ремонтируют правкой.
Для
определения величины изгиба корпус
подлежит разметке.
Для
этого находят и обозначают середину
хвостовика на расстоянии 20 мм от упора,
а также в средней части и на торце. Затем
соединяют линией точки, обозначающие
середину хвостовика. Изгибом является
отклонение указанной линии от середины
хвостовика в его средней части.
Правке
подлежат изгибы более 3 мм как в
вертикальной, так и в горизонтальной
плоскостях. Если в зонах изгибов имеются
заваренные или не заваренные трещины,
то корпус подлежит сдаче в металлолом.
Правку
выполняют с предварительным нагревом
до температуры 800 – 850°C с выдержкой в
печи не менее 1 часа для равномерного
прогрева корпуса. Заканчивать правку
необходимо при температуре выправляемых
зон не менее 650°C для предотвращения
образования термических трещин.
Правку
производят на специализированных
гидравлических прессах. При устранении
уширения зева в корпус вставляют
ограничитель, исключающий сужение зева
больше нормы.
Охлаждение
корпусов производят в помещениях при
отсутствии сквозняков, не применяя воду
или другую охлаждающую среду.
Трещины
и износы, выявленные в корпусе автосцепки,
ремонтируют сваркой и наплавкой.
Разрешается при всех видах ремонта
вагонов:
—
заваривать вертикальные трещины сверху
и снизу в углах зева, если они не выходят
за положение верхнего или нижнего зуба;
—
заваривать трещины в углах окон для
замка и замкодержателя, если после
разделки трещины в верхней части не
выходят на горизонтальную поверхность
головы и за положение верхнего ребра
со стороны большого зуба, а в нижней
части имеют длину не более 20 мм;
—
вырубать трещины глубиной до 5 мм в
хвостовике корпуса с плавным переходом
на поверхность без заварки. Трещины
перемычки глубиной не более 8 мм можно
заваривать при условии, что после их
разделки толщина перемычки будет не
менее 40 мм;
—
заваривать трещину перемычки между
отверстиями для направляющего зуба и
сигнального отростка замка, если трещина
не выходит на вертикальную стенку
корпуса;
—
заваривать трещину хвостовика автосцепки.
Общая длина ремонтируемых трещин
хвостовика в зоне от упора до передней
кромки отверстия для клина не более 100
мм у корпусов, проработавших свыше 20
лет и более 150 мм для остальных корпусов;
—
наплавлять изношенные поверхности 6
контура зацепления так чтобы сварочные
швы не доходили до мест закруглений
ближе 15 мм.
Переход
от отремонтированной наплавкой ударной
поверхности стенок зева к неизношенной
должен быть плавным, по длине не менее
15 мм. Твердость наплавленного металла
ударно-тяговых поверхностей должна
быть не менее 250 НВ для грузовых вагонов
и не менее 450 НВ для пассажирских и
рефрижераторных. Для обеспечения
необходимой твердости наплавку следует
выполнять электродами ОЗН-400, порошковой
проволокой ПП-ТН350, ПП-ТН500 или пластичными
электродами с использованием легирующих
присадок.
Разрешается
при всех видах ремонта:
—
наплавлять поверхности корпуса,
соприкасающиеся при работе с центрирующей
болочкой, тяговым хомутом, ударной
розеткой и клином тягового хомута при
износе более 3 мм, но не более 8 мм;
—
наплавлять изношенную полочку
предохранителя и шип для замкодержателя
или приваривать новые в случае их излома;
—
наплавлять оба изношенных отверстия
для валика подъемника;
—
наплавлять места опоры стенки
замкодержателя на корпус, нижней
перемычки в окне для замка и задней
наклонной части дна карманов;
—
наплавлять изношенный торец хвостовика,
если его длина менее 645 мм для автосцепки
СА-3 и менее 654 мм для автосцепки СА-3М;
—
наплавлять изношенную перемычку
хвостовика, если ее толщина в средней
части не менее 40мм – для СА-3М.
Разделка
кромок трещин производится с применением
ручного или пневматического зубила,
электродуговой или газокислородной
резкой. При ремонте трещин в зеве
необходим подогрев головы автосцепки
до температуры 250 – 300°C, что улучшает
качество наплавленного металла и снижает
термические напряжения.
Ограничители
вертикальных перемещений вагонов не
должны иметь изгибов и износов более 5
мм. Автосцепки вагонов для перевозки
опасных грузов оборудованы как нижними,
так и верхним ограничителями.
В
деталях механизма автосцепки при всех
видах ремонта вагонов разрешается:
У
замка наплавка изношенной поверхности
замыкающей части , овального отверстия
при износе не более 8 мм, направляющего
зуба , поверхности радиальной опоры,
шипа для предохранителя. В случае излома
шипа или сигнального отростка допускается
их приварка. Твердость направленного
металла замыкающей части замка должна
быть не менее 250 НВ, а для пассажирских
и рефрижераторных вагонов – не менее
400 – 450 НВ. Замыкающие части замков
рекомендуется упрочнять контактно
-дуговой сваркой, что значительно
повышает их износостойкость. Упрочнение
замка происходит в результате воздействия
электрической дуги и переноса на
замыкающую часть материала электрода,
в качестве которого используют роликовые
подшипники из стали ШХ-15СГ;
У
замкодержателя заваривать не более
одной трещины; наплавлять изношенные
поверхности противовеса , отверстия ,
лапы , расцепного угла ; править погнутые
детали в нагретом состоянии до температуры
820 – 900°C;
В
предохранителе замка наплавлять износы
верхнего плеча и отверстия под шип замка
, править изгибы плеч в нагретом состоянии;
В
подъемнике замка наплавлять изношенные
поверхности широкого пальца , узкого
пальца , квадратного отверстия ;
У
валика подъемника наплавлять изношенные
поверхности квадрата, цилиндрические
поверхности и стенки паза болта.
Обработка
наплавленных поверхностей деталей
автосцепки производится с применением
фрезерных, строгальных станков,
шлифовальных машинок и специализированной
оснастки.
Правку
погнутых деталей механизма осуществляют
с использованием специальных штампов.
После
ремонта детали и автосцепки в сборе
проверяют шаблонами и в случае соответствия
ее требованиям приемки, валик подъемника
закрепляют болтом с гайкой, под головку
болта и гайку ставят фасовочные шайбы,
которые загибают на головку болта и
гайку.
Соседние файлы в предмете [НЕСОРТИРОВАННОЕ]
- #
- #
- #
- #
- #
- #
- #
- #
- #
- #
- #
Краткое описание: В статье рассмотрим основные проблемы автосцепки SA 3 и дадим пошаговую инструкцию по ее ремонту. Вы узнаете, как определить неисправность, как разобрать и собрать автосцепку, а также какие особенности ремонта у этой модели.
Статья:
Автосцепка SA 3 – важный элемент грузового автомобиля, который обеспечивает безопасность и надежность при перевозке грузов. Но как и любая деталь, она может выйти из строя со временем. Неисправность автосцепки SA 3 может проявляться разными способами: затрудненное подключение прицепа, плохой контакт, шумы и вибрации во время движения.
Как определить неисправность автосцепки SA 3
Перед тем, как приступить к ремонту, нужно определить причину неисправности. Для этого проведите визуальный осмотр автосцепки. Проверьте наличие трещин, сколов, износа. Если деталь негодна, ее нужно заменить.
Если внешних повреждений нет, необходимо проверить качество соединения прицепа с автомобилем. Выясните, возникает ли зазор между защелкой и тягово-сцепным устройством. Проверьте подшипник и убедитесь в том, что не существует повреждений или трещин.
Разборка и сборка автосцепки SA 3
Перед тем как начать разборку, следует отключить тягово-сцепное устройство от автомобиля. Наиболее распространенной причиной неисправности автосцепки SA 3 являются загрязнения. Отключив всю связь между прицепом и автомобилем, следует осмотреть и почистить все детали сцепления.
Итак, первым шагом разборки является снятие задней крышки автосцепки, которая защищает ее от пыли и грязи. Затем, следует снять кольцо фиксации штока и вытащить шток из автосцепки. Теперь можно вынуть палец со штока.
После разборки нужно тщательно проверить состояние деталей. Проверьте стыки, подшипники, замените пыльники и прочистите трещины сцепления от грязи и мусора.
После того, как все детали почищены и смазаны, можно приступать к сборке автосцепки. Сначала вставьте палец в отверстие штока и надежно закрепите его при помощи кольца фиксации. После установите шток в свое место и закрепите его задней крышкой.
Особенности ремонта автосцепки SA 3
Ремонт автосцепки SA 3 может быть более сложным, чем у других моделей. Например, при необходимости замены подшипников или штока, необходимо вскрытие почти всего механизма. Некоторые детали автосцепки могут быть дорогими и труднодоступными. Поэтому, если есть даже небольшие проблемы с автосцепкой SA 3, следует обращаться к профессионалам, которые смогут быстро и качественно провести ремонт этой модели.
В заключение, хочется подчеркнуть, что ремонт автосцепки SA 3 может быть необходимым важным мероприятием для безопасности водителя и всего транспорта. Следование нашей инструкции поможет вам быстро и качественно устранить проблемы с автосцепкой SA 3. Однако, если по какой-то причине, ремонт сцепки кажется вам слишком сложным, не стоит рисковать и лучше доверить исправление профессионалам.
Переместить автосцепку СА-3 на позицию ремонта.
Автосцепку в кассету установить, разобрать, для чего: повернуть автосцепку большим зубом вниз, разогнуть шайбу под гайкой, отвинтить гайку с болта и вынуть болт, повернуть автосцепку в рабочее положение, вынуть детали механизма, уложить на стенд для контроля деталей.
Перед электросварочными работами обратить внимание на маркировку корпуса автосцепки:
“Т”- углеродистая сталь с термоупрочнением;
“ТТ”- сталь марки 20ГЛ с термоупрочнением;
“С”- сталь с содержанием углерода более 0.25%, автосцепка требует подогрева до 250-300о С перед сваркой;
“НЛ”- низколегированная сталь.
Установить в кассету корпус автосцепки и повернуть в рабочее положение.
Установить в кассету корпус автосцепки и повернуть в рабочее положение.
Произвести дефектацию корпуса автосцепки
Трещина в зеве корпуса (деф.1)
Не выходящая за горизонтальную поверхность — ремонтировать Выходящая за горизонтальную поверхность – заменить
Трещина в зеве корпуса (деф.2)
Не выходящая за положение верхнего ребра со стороны большого зуба – ремонтировать
Выходящая за положение верхнего ребра со стороны большого зуба – заменить
Трещина в зеве корпуса (деф.3)
Длиной (после разделки) не более 20 мм – ремонтировать
Длиной (после разделки) более 20 мм – заменить
Трещины в углах со стороны большого зуба головки по вертикали сверху и снизу
(деф.9,10)
Не выходящие каждая из них за положение верхнего или нижнего ребра со стороны большого зуба – ремонтировать
Выходящие каждая из них за положение верхнего или нижнего ребра со стороны большого зуба – заменить
Трещины в перемычке хвостовика (деф.7)
Глубиной не более 5 мм при условии, что толщина перемычки хвостовика после вырубки
Не менее 40 мм – ремонтировать
Менее 40 мм – заменить
Мелкие (сетчатые) глубиной не более 8 мм при условии, что толщина перемычки хвостовика после вырубки
Не менее 40 мм – ремонтировать
Менее 40 мм – заменить
Трещина в перемычке между отверстием для сигнального отростка замка и отверстием для направляющего зуба замка
Не выходящие на вертикальную стенку кармана — ремонтировать
Выходящие на вертикальную стенку кармана – заменить
Уширение зева корпуса (деф.5)
Ремонтировать
Износ тяговой поверхности головки (деф.11,14)
Большого зуба – ремонтировать
Малого зуба – ремонтировать
Износ ударной поверхности головки (деф.12,13).
Большого зуба – ремонтировать
Малого зуба – ремонтировать
Несоответствие контура зацепления требованиям шаблона
Ремонтировать
Несоответствие углов зева и малого зуба корпуса шаблону
Ремонтировать
Уширение кармана для замка
Ремонтировать
Износ отверстия для запорного болта валика подъемника
Ремонтировать
Износ отверстий для валика подъемника и их положение относительно контура зацепления
Ремонтировать
Дефекты шипа для замкодержателя
Излом шипа — ремонтировать
Несоответствие высоты шипа требованиям шаблона — ремонтировать
Несоответствие диаметра и состояния кромки шипа требованиям шаблона – ремонтировать
Несоответствие положения передней поверхности шипа относительно контура зацепления – ремонтировать
Излом полочки для верхнего плеча предохранителя
Ремонтировать
Несоответствие положения полочки для верхнего плеча предохранителя в корпусе относительно шипа для замкодержателя и контура зацепления
Ремонтировать
Износ хвостовика автосцепки по месту прилегания его к тяговому хомуту, ударной розетке, центрирующей балочке
(деф.16)
Глубиной до 3 мм — без ремонта
Более 3,но не более 8 мм – ремонтировать
Более 3,но более 8 мм – заменить
Толщина перемычки хвостовика менее 40 мм
Заменить
Износ стенок отверстия в хвостовике (деф.8)
По длине при толщине перемычки хвостовика
Более 40 мм – ремонтировать
Менее 40 мм – заменить
По ширине износа на глубину до 3 мм — без ремонта
Более 3,но не более 8 мм — ремонтировать
более 8 мм — заменить
Износ торцевой части хвостовика (деф.6)
При длине хвостовика до 645 мм – без ремонта
Менее 645 мм – ремонтировать
Изгиб хвостовика (деф.17)
Расстояние от первоначальной продольной оси корпуса в средней части не превышает 3 мм — без ремонта.
Превышает 3мм и в зоне изгиба нет заваренных и не заваренных трещин– заменить. Превышает 3мм и в зоне изгиба есть заваренные или не заваренные трещины – заменить
Корпус автосцепки сроком службы 20 и более лет
Заменить
Трещины в зоне “А” хвостовика (деф.15)
Площадью поперечного сечения хвостовика после вырубки
Не более 25% — ремонтировать
Более 25% — заменить
Трещины по всему корпусу суммарной длиной более 100 мм — заменить
Трещина в месте перехода от головки к хвостовику (деф.18)
Глубиной не более 15 мм и длиной до 150 мм – ремонтировать
Глубиной более 15 мм или длиной более 150 мм – заменить
Корпус автосцепки подвергается дефектоскопированию на наличие трещин (деф.1,2,3,4,7,9,10)
Деф.1,2,3,4,7,9,10,15,18.
Разделать трещины. Допускается разделка трещин: механическим способом, электродуговым или специальными электродами и поверхностно-кислородной резкой. Разделка трещин воздушно-дуговым способом угольным электродом не допускается. Сила тока при разделке трещин: 350-380 А для электродов типа Э42 диаметром 5 мм. Трещины в корпусе глубиной до 5 мм можно выводить плавной выпиловкой без заварки. Разделать первичные трещины (деф.15,18) на глубину 10-12 мм, длиной 5-10 мм больше от концов видимой части трещины.
Разделать повторные трещины (деф.15,18), образовавшиеся по ранее выполненному сварочному шву, на полную толщину стенки хвостовика оставляя перемычку в корне разделки толщиной 2-4 мм. Длина разделки на 5-10 мм больше от концов ранее заваренного шва. Удалить наплавленный металл. В случае сквозного прожога стенки хвостовика производить заварку прожженного места электродами 3 мм током 110-130 А до образования перемычки.
Разделать первичные трещины в верхнем (деф.1) и нижнем (деф.4) углах окна для замка на полную глубину залегания трещины длиной на 5-8 мм больше, чем длина видимой трещины. Разделать первичные трещины в верхнем (деф.2) и нижнем (деф.3) углах окна для замкодержателя от конца с выходом в окно на глубину 20 мм. Разделать повторные трещины в углах (деф.1,2,3,4), образовавшиеся по ранее выполненному шву, на полную глубину залегания трещины и длиной на 5-8 мм больше, чем длина ранее выполненной заварки. Удалить наплавленный металл. Разделать трещины (деф.9,10) и трещины в перемычке между отверстиями для сигнального отростка и направляющего зуба замка на полную глубину их залегания.
После разделки к заварке допускаются трещины: (деф.1)- не выходящие на верхнюю горизонтальную поверхность; (деф.2)- не выходящие за положение верхнего ребра большого зуба; (деф.3,4)- не длиннее 20 мм; (деф.9,10)- не выходящие за верхнюю и нижнюю горизонтальные плоскости наружных ребер большого зуба. Нагреть завариваемое место корпуса до температуры 250-300оС. Заварить трещины на корпусе. В случае длительного перерыва и остывания места сварки ниже 250о С греть повторно, продолжать заварку. В случае, если разделка трещин производится электродуговым способом или поверхностно-кислородной резкой и заварка её выполняется сразу после разделки, то предварительный подогрев не обязателен.
Производится электродуговым способом или поверхностно-кислородной резкой и заварка ее выполняется сразу после разделки, то предварительный подогрев необязателен.
Заварить трещины в нижнем горизонтальном положении, удалять шлак после наложения каждого шва. Выводить кратер на наплавленный металл и заваривать. Усиление шва должно быть в пределах 1.5-2.0 мм и иметь плавный переход к основному металлу.
Непровары в корне шва не допускаются.
Контролировать температуру подогрева.
Деф.11,12,13,14
Наплавить рабочие поверхности контура зацепления ЦВ-4006.
Наплавленный металл не должен доходить ближе 15 мм к закруглениям в углах. Толщина наплавленного слоя на ударные поверхности (деф.13,12) определяются величиной зазора “а” и “б” между наплавляемой поверхностью и ребром профильной планки 914р/24-1м. Для определения наибольшей допускаемой толщины наплавки на тяговую поверхность (деф.14) надо из величины зазора “в” между ребром шаблона 914р/22-м, плотно прижатого к ударной поверхности малого зуба, и тяговой поверхностью вычесть величину, ранее определенного с помощью шаблона 914р-м зазора “а”. Для определения толщины наплавки на тяговую поверхность (деф.11) надо из величины зазора “г” между ребром шаблона 914р/25, плотно прижатого к ударной поверхности зева, и тяговой поверхностью вычесть величину ранее определенного с помощью шаблона 914р-м зазора “б”.
Режим наплавки: ток 280-310 А, постоянный, обратная полярность, напряжение на дуге 27-29 В, скорость подачи проволоки 126 м/час, вылет электродной проволоки 50 мм.
Очистить наплавленные места от шлаковой корки, вырубить дефектные места шва после наплавки.
Контроль исполнителем.
Установить корпус в удобное положение для наплавки отверстия болта, крепящего валик подъемника.
Наплавить паз для болта заподлицо с поверхностью задней кромки отверстия.
Наплавить малое отверстие для валика подъёмника.
Толщину наплавляемого слоя контролировать шаблонами.
Наплавить большое отверстие для валика подъёмника.
Перед наплавкой в отверстие для болта, крепящего валик подъёмника, вставить медный пруток.
Установить корпус горизонтально, большим зубом вниз.
Проверить ширину кармана в месте установки шайбы шаблонами и подобрать необходимую по толщине шайбу. ЦВ — 4006 п.2.1.1.
Установить шайбу в кармане корпуса и приварить.
Наплавить верхнюю цилиндрическую поверхность шипа для замкодержателя.
Толщину наплавляемого слоя контролировать шаблонами.
Установить корпус в кассете, наплавлять (через окно для замка).
При наплавке корпус перемещать в вертикальное положение.
Установить корпус горизонтально, карманом для замка вверх.
Наплавить нижнюю цилиндрическую поверхность шипа (через отверстие для сигнального отростка ). При наплавке корпус перемещать в вертикальное положение.
Установить корпус горизонтально большим зубом вниз.
Наплавить торец шипа.
Проверить высоту наплавки.
Проходная сторона шаблона должна проходить между торцом шипа (наплавленного) и вертикальной стенкой кармана замка.
Установить корпус под углом 450 , нижней частью кармана вверх.
Установить на полочку медную пластину так, чтобы она одним выступом легла на рабочую поверхность полочки, другим выступом уперлась в серповидный прилив и пружиной — в потолок корпуса.
Наплавить переднюю поверхность полочки и, сняв пластину из кармана, наплавить серповидный прилив.
Поставить корпус в горизонтальное положение.
Зачистить рабочие поверхности после наплавки. Проверить положение полочки шаблоном.
Установить корпус в вертикальное положение, хвостовиком вниз.
Срезать неисправную полочку или оставшуюся её часть заподлицо с внутренней стенкой кармана корпуса; не повредить при этом серповидный прилив.
Удалить застывшие брызги металла.
Поставить новую полочку в приспособление ; установить приспособление в корпусе и приварить полочку. Снять приспособление с корпуса. Заплавить зазор “а” между серповидным приливом “б” и полочкой “в”; зазор остается без заварки, если его величина не превышает 3 мм. зазор более 3 мм разделать до величины 8-10 мм (частичной срезкой серповидного прилива) и заварить; произвести подварку полочки контрольным швом через окно для сигнального отростка.
Проверить прочность приварки (после остывания) ударами молотка весом в 1 кг по металлическому стержню, который концом упирается в полочку.
Удары должны наноситься достаточно сильно, но чтобы не погнуть приваренную полочку. Полочка должна располагаться перпендикулярно к внутренней стенке малого зуба; допускается отклонение не более 2мм, измеряемое по концу полочки. Проверить положение полочки относительно контура зацепления.
Установить корпус вертикально, хвостовиком вниз.
Срезать неисправный серповидный прилив заподлицо с внутренней стенкой кармана. Удалить наплывы и неровности. Поставить новый серповидный прилив с полочкой в приспособление. Новый серповидный прилив с полочкой изготовить по чертежу.
Установить приспособление в корпусе; приварить серповидный прилив к стенке кармана; снять приспособление с корпуса; приварить серповидный прилив с полочкой с другой стороны; наложить контрольный шов со стороны зева.
Проверить прочность приварки (после остывания) ударами молотка весом в 1 кг по металлическому стержню, который концом упирается в полочку.
Удары должны наноситься достаточно сильно, но чтобы не погнуть приваренную полочку. Полочка должна располагаться перпендикулярно к внутренней стенке малого зуба; допускается отклонение не более 2мм, измеряемое по концу полочки. Проверить положение полочки относительно контура зацепления.
Деф. 6.
Установить корпус вертикально, хвостовиком вверх.
Наплавить торец хвостовика; наплавка производится если длина хвостовика менее 645 мм.
Деф. 8.
Установить корпус вертикально, хвостовиком вниз, затем под углом.
Наплавить перемычку хвостовика; наплавка разрешается при толщине перемычки перед наплавкой не менее 40 мм; наплавку следует производить в последовательности А, Б, В КЭ .
Установить корпус в горизонтальное положение и наплавить боковые стенки отверстия. Далее, установить корпус горизонтально, наплавляемой поверхностью кверху и наплавить изношенные места. Наплавлять разрешается при износе глубиной свыше 3 мм, но не более 8 мм.
Повернуть корпус другой плоскостью и наплавить места износов.
Установить корпус горизонтально.
Наплавить нижнюю перемычку малого зуба “б” и заднюю наклонную часть для кармана в корпусе, в месте опоры замка “в” (необходимость наплавки этих мест устанавливается после сборки механизма автосцепки).
Наплавка нижней перемычки производится, если расстояние от вертикальной кромки малого зуба до замка при его свободном положении менее 2 мм; толщина наплавки допускается от 3 до 6 мм с последующей обработкой.
Наплавка задней наклонной части кармана в месте опоры замка, если расстояние от вертикальной кромки малого зуба до замка при его свободном положении более 8 мм; толщина наплавки допускается от 3 до 6 мм с последующей обработкой наплавленной поверхности через нижнее большое окно корпуса.
Установить корпус в кассете горизонтально, отверстием для сигнального отростка вверх и наплавить место опоры шейки замкодержателя с внутренней стороны (необходимость наплавки устанавливается после сборки механизма автосцепки). Наплавка производится если расстояние от кромки лапы замкодержателя по горизонтали менее 20 мм, а для замкодержателей, не имеющих скоса лапы, не менее 9 мм.
Установить корпус автосцепки.
Обработать ударную стенку зева. Проверить правильность обработки ударной стенки зева (Инструкция п. 2.1.5.).
Браковать, если непроходной щуп по всей своей ширине проходит ( до упора в прилив рукоятки) в зазор между профильной планкой, плотно прижатой по концам к контурным местам шаблона и проверяемой поверхностью; разность зазоров между профильной планкой и ударными плоскостями малого зуба и зева вверху и внизу не должна превышать 2 мм; зазор между профильной планкой и ударной стенкой зева в зоне, лежащей ниже большого зуба не контролируется.
Обработать ударную поверхность малого зуба в соответствии с контуром чертежам.
Проверить корпус КЭ .
Проверить закругления малого зуба КЭ .
Обработать тяговую поверхность малого зуба под шаблон (Инструкция п.2.1.2; п.2.1.4). Малый зуб должен быть проверен по всей высоте вертикальных площадок тяговой и ударной т.е. на расстоянии 80 мм вверх и вниз от литейного шва.
Проверить малый зуб шаблонами (Инструкция п.2.1.6; п.2.1.8).
Проверить контур зацепления. Контур зацепления считается годным, если шаблон свободно проходит через него по всей высоте.
Поставить и закрепить корпус на стенде. Установить приспособление для обработки отверстий на корпусе автосцепки.
Обработать оба отверстия для валика; обработку производить с охлаждением фрез эмульсией.
Проверить диаметры и соосность отверстий для валика подъёмника. Отверстие считается исправным, если проходные части шаблона входят в соответствующие отверстия, а непроходные – не входят. Для проверки шаблон 937р вводят в карман корпуса, а через отверстие этого шаблона пропускают шаблон 797р; отжимая шаблон к внутренней стенке и нижней перемычки малого зуба, перемещают его, проверяя величину зазора между упором и ударной стенкой зева. Положение отверстия правильное, если зазор не более 4 мм. Снять корпус автосцепки со стенда.
Установить корпус автосцепки головкой вниз.
Разметить торец хвостовика для обработки. Обработать торец хвостовика. Проверить хвостовик шаблонами. Проверка производится со стороны верхней и нижней плоскости (Инструкция п.2.1.15). Зачистить наплывы от наплавки и заусенцы, выходящие на боковые стенки хвостовика.
Поставить корпус автосцепки на стенд большим зубом вниз; установить оправку, с насаженными на неё 3-мя фрезами. На хвостовике автосцепки и закрепить.
Соединить оправку с шарнирным валом привода, включить электродвигатель и обработать отверстие для клина. Затем выключить электродвигатель и снять приспособление.
Проверить перемычку хвостовика и боковые поверхности отверстия для клина; обработанная поверхность перемычки со стороны клина должна быть ровной с радиусом кривизны не менее 16 мм и не более 20 мм; раковины и подрезы в местах сопряжения основного и наплавленного металла не допускаются.
Проверить перемычку с обеих сторон; толщина после обработки должна быть 50,5 – 53мм
Снять корпус автосцепки со стенда.
Установить корпус в положение, удобное для зачистки.
Зачистить места наплавки хвостовика; зачистить рабочие поверхности контура зацепления.
А также зачистить углы зева малого и большого зубьев.
Проверить углы зева и малого зуба (Инструкция п.2.1.9).
Проверить рабочие поверхности контура зацепления корпуса (Инструкция п.2.1.7).
Повернуть корпус автосцепки карманом вверх.
Зачистить (через отверстие в кармане ) наплавку на нижней перемычке кармана.
Проверить положение замка в кармане корпуса (Инструкция п.2.1.38а).
Торцевая поверхность замка, установленного в карман корпуса вместе с валиком подъёмника, должна находиться от вертикальной кромки малого зуба на расстоянии 2-8 мм.
Установить корпус горизонтально, большим зубом вниз.
Зачистить наплавку на внутренней поверхности стенки зева в месте опоры шейки замкодержателя; зачистить внутреннюю стенку заподлицо с неизношенной поверхностью.
Проверить положение замка и замкодержателя в кармане корпуса (Инструкция п.2.1.38а); расстояние от кромки замка до кромки лапы замкодержателя по горизонтали должно быть не менее 20 мм; замеры производить при свободном положении замка.
Зачистить наплавку паза для запорного болта в отверстии для валика подъёмника; зачистить заподлицо с поверхностью задней кромки отверстия.
Проверить положение отверстия для запорного болта (Инструкция п.2.1.11).
Для этого шаблон устанавливается так, чтобы прямолинейная поверхность непроходной планки его входила в паз для запорного болта, при этом полукруглая поверхность шаблона не должна пройти мимо передней кромки отверстия для валика подъёмника.
Проверить после обработки вновь просверленное отверстие шаблоном с установкой запорного болта, который должен свободно входить на своё место и легко извлекаться.
Произвести дефектацию замка :
Изгиб корпуса замка (деф. 10)
Заменить
Трещина в верхней перемычке замка (деф.6).
Ремонтировать.
Износ замыкающей части замка (деф.1).
Ремонтировать.
Износ задней кромки овального отверстия (деф.5).
Не более 8 мм – ремонтировать
Более 8 мм – заменить
Износ диаметра шипа для предохранителя (деф.8).
Ремонтировать
Несоответствие места расположения шипа (деф.8)
Ремонтировать
Излом шипа для предохранителя (деф.9).
Ремонтировать
Износ прилива для шипа (деф. 7).
Не более 3 мм – без ремонта
Более 3 мм – ремонтировать
Износ направляющего зуба (деф.3).
При суммарном зазоре не более 2 мм – без ремонта
Более 2 мм — ремонтировать
Изгиб сигнального отростка (деф.2).
Заменить
Излом сигнального отростка (деф.2).
Ремонтировать
Деф. 1
Установить замок в приспособление и наплавить замыкающую поверхность. Затем снять замок с приспособления и очистить от брызг металла и шлака.
Деф.5.
Установить замок сигнальным отростком в гнездо приспособления; наплавить заднюю кромку овального отверстия. Снять замок и очистить от брызг металла и шлака.
Деф.8, 7, 6.
Наплавить шип для предохранителя; наплавить прилив шипа. Сломанный шип, поставленный на резьбе, привернуть. Обварить по диаметру.
Деф.3.
Наплавить нижнюю опорную часть и направляющий зуб.
Установить приспособление на фрезерный станок; закрепить его.
Установить замок на приспособление; закрепить его.
Обработать замыкающую поверхность замка.
Затем, зачистить заусенцы и наплывы, выходящую на торцевую поверхность. Проверить толщину замыкающей части (Инструкция п.2.1.22).
Установить замок в приспособление.
Обработать заднюю кромку овального отверстия. Зачистить боковые кромки овального отверстия.
Проверить положение задней кромки овального отверстия относительно торца замка (Инструкция п.2.1.23). Замок считается годным, если проходная часть мерительного сектора свободно проходит мимо кромки отверстия замка, а непроходная часть не проходит (упирается в кромку отверстия).
Обработать цилиндрическую часть шипа, торец шипа, прилив шипа. На обработанной поверхности раковины и непровары не допускаются; переход поверхности шипа к плоскости замка должен быть скруглен радиусом 2-3 мм.
Проверить положение, диаметр и прилив шипа.
Поставить и закрепить в патроне пруток и в суппорте резцы.
Нарезать резьбу М-22 длиной 17±0,2 мм и отрезать шип; длина шипа вместе с резьбой 42 мм.
Разметить центр шипа на замке и накернить.
Закрепить сверло в шпинделе станка и просверлить отверстие в замке. Далее, поставить зенкер и снять фаску 4х45 0.
Поставить метчик и нарезать резьбу.
Ввернуть шип в замок и заварить.
Зачистить. Обработать на заточном станке нижнюю опорную часть и направляющий зуб. Проверить шаблоном направляющий зуб (Инструкция п.2.1.24).
Определить размер обломанного конца сигнального отростка.
Разметить и отрезать заготовку, разделать швы под сварку на сигнальном отростке и замке. Приварить сигнальный отросток. Зачистить места сварки. Проверить замок шаблоном (Инструкция п.2.1.25а).
Окрасить сигнальный отросток в красный цвет, зачистить старое клеймо и поставить новое клеймо (Инструкция п.2.7.).
Произвести дефектацию замкодержателя:
Трещина замкодержателя (деф.5).
Одна трещина – ремонтировать
две и более трещины – заменить
Заусенцы, наплывы металла (деф.6).
Ремонтировать
Изгиб корпуса замкодержателя (деф.7)
Заменить
Износы:
ширины лапы (деф.3) – ремонтировать
упорной поверхности противовеса (деф.4) — ремонтировать
стенок овального отверстия (деф.2) — ремонтировать
Несоответствие контуру шаблона, зазор между профильной призмой и выступом шаблона:
Не более 1мм — без ремонта
более 1мм – ремонтировать
Деф.1, 2, 3, 4, 5.
Наплавить изношенные места замкодержателя; упорную поверхность противовеса, стенки отверстия, ширину лапы, расцепной угол.
Трещину разделать и заварить. Очистить наплавленные места от брызг металла и шлака.
Обработать наплавленные стенки овального отверстия.
Проверить шаблоном отверстие овальное по ширине и длине; длина допускается, если замкодержатель не надевается на непроходную часть пробки; ширина допускается, если замкодержатель не надевается отверстием на непроходную пробку или надевается частично, но не доходит до упора до упора в лист шаблона. Обработать после наплавки упорную поверхность противовеса.
Обработать лапу; зачистить заусенцы (деф.6).
Проверить шаблоном. Проверить шаблоном упорную поверхность противовеса. Зачистить верх упорной поверхности противовеса. Проверить шаблоном высоту угла противовеса; высота угла противовеса правильная, если проходная часть планки поворачиваясь по часовой стрелке проходит мимо угла противовеса, а непроходная часть планки не проходит. Обработать расцепной угол; зачистить заусенцы. Проверить шаблоном; расцепной угол годен, когда проходная часть сухаря, поворачиваемого против часовой стрелки, проходит мимо угла, а непроходная — не проходит.
Проверить контур замкодержателя шаблоном; замкодержатель годен, если его боковая стенка плотно лежит на плите шаблона, а профильная призма шаблона своим выступом касается упора или зазор между ними не превышает 1 мм. Зачистить старое клеймо, поставить клеймо депо (Инструкция п.2.7.).
Произвести дефектацию предохранителя замка:
Трещина предохранителя (деф.3).
Заменить
Излом плеча предохранителя (деф.4).
Заменить
Изгиб предохранителя (деф.5).
Заменить
Износ верхнего плеча предохранителя (деф.1).
Ремонтировать
Износ отверстия предохранителя (деф.2).
Ремонтировать
Деф.1,2.
Установить предохранитель на приспособление так, чтобы верхнее плечо его опиралось на упор, а нижнее прижать планкой. Наплавить верхнее плечо по высоте и толщине торцевой поверхности; наплавить отверстие.
Разметить центр заваренного отверстия и накернить.
Поставить и закрепить сверло Æ 24 мм в патроне станка; установить предохранитель на столе станке. Просверлить отверстие, заменить сверло и Æ 24 на Æ 30 мм ; снять фаску 3х450 со стороны плоскости, обращенной к замку; снять предохранитель.
Укрепить предохранитель на станке; закрепить резец в резцедержателе суппорта.
Обработать торец верхнего плеча. Снять предохранитель с приспособления.
Обработать торец верхнего плеча: высоту торца и боковые поверхности.
Проверить предохранитель (Инструкция п.2.1.33).
Предохранитель считается исправным если он:
А). не надевается на пробку с обеих сторон или надевается не неё, но не доходит до упора в лист шаблона;
Б). Нижним углом торца верхнего плеча проходит мимо проходной части сухаря и не проходит мимо непроходной;
В). торцевой частью верхнего плеча не полностью входит в вырез до упора в заднюю стенку выреза, т.е. остается зазор.
Зачистить старое клеймо и поставить новое.
Произвести дефектацию подъёмника замка:
Износ поверхности узкого пальца (деф.1).
Ремонтировать
Износ поверхности широкого пальца (деф.2).
Ремонтировать
Износ стенок квадратного отверстия (деф.3).
Ремонтировать
Заусенцы, наплывы металла (деф.4).
Ремонтировать
Деф.1, 2, 3, 4.
Установить подъёмник замка на приспособление и наплавить изношенные места.
Очистить наплавленные места от брызг металла и шлака.
Обработать наплавленные поверхности.
Зачистить заусенцы, наплывы металла (деф.4).
Проверить подъёмник замка после ремонта. Подъёмник считается исправным если:
А). Надетый на пробку входит в обойму;
Б). Проходит в вырез;
В). буртиком входит в вырез;
Г). отверстием не надевается на пробку “Не”;
Д). Надетый на пробку “Пр” не подходит широким пальцем под головку стойки, а узким пальцем проходит мимо проходной части сухаря и не проходит мимо непроходной.
Далее, зачистить старое клеймо.
Поставить клеймо (Инструкция п.2.7.).
Произвести дефектацию валика:
Износ цилиндрической поверхности стержня малого диаметра (деф.1)
Ремонтировать
Износ поверхности квадрата (деф.2).
Ремонтировать
Износ стенок паза для запорного болта (деф.3)
Ремонтировать
Автосцепка СА-3 — это автоматическое ударно-тяговое сцепное устройство не жесткого типа, служащее для сцепления элементов подвижного состава между собой. К деталям автосцепки СА-3 относят: корпус автосцепки, замок, замкодержатель, предохранитель замка, подъемник замка, валик подъемника. Автосцепка СА-3 и унифицированные с ней детали могут иметь дополнительные устройства и конструктивные исполнения, исходя из требований к конкретной единице железнодорожного подвижного состава.
Механизм автоматического соединения позволяет вагонам присоединяться друг к другу и упрощает процедуру сцепки и расцепки. Центральное расположение сцепки на вагоне обеспечивает равномерное распределение нагрузки между вагонами, что способствует устойчивости и стабильности поезда в движении.
Меню страницы:
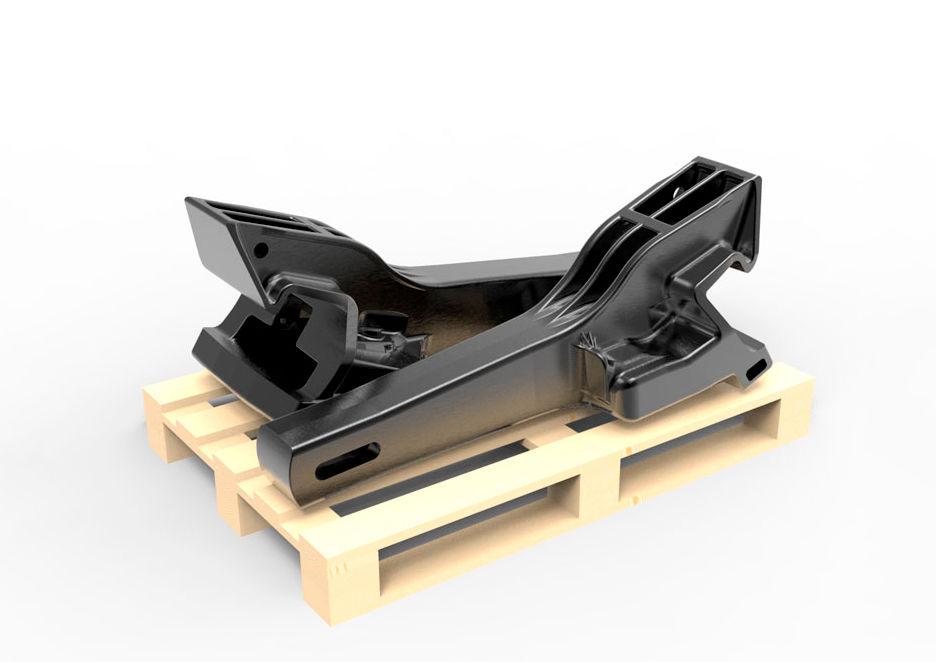
Конструкцией автосцепки модели СА-3, массово применяемой на железных дорогах более 70 лет без существенных изменений, обеспечиваются сцепление и исключение разъединения вагонов при движении поезда в случае, если перед сцеплением разница по высоте между автосцепками не превышает 100 мм. Причиной такого ограничения является необходимость обеспечить достаточную величину площадки перекрытия замков. При превышении установленной разницы сцепление будет ненадежным, и при проходе по криволинейным участкам пути может произойти саморасцеп.
⟦Устройство и назначение⟧
Автосцепное устройство представляет собой комплект сборочных единиц и деталей для автоматического сцепления единиц подвижного состава, удержания их на определенном расстоянии друг от друга, а также передачи и амортизации продольных сил. Для автосцепных устройств существует ограничение, вызванное особенностью их конструкции. Данное ограничение заключается в обеспечении автоматического сцепления вагонов только в случае не превышения определенной величины разности высот уровней осей сцепляемых автосцепок. Это ограничение позволяет учесть возможные понижения конструкции вагона после его изготовления за счет износов, прогиба рессорного подвешивания и допусков установки.
Корпус автосцепки отливается из углеродистой стали мартеновского производства, которая, согласно ГОСТ 88-55, имеет углерода 0,17-0,27%, марганца 0,5-0,9%, кремния 0,17-0,37%, серы и фосфора не более 0,045% каждого. Минимальные значения механических характеристик составляют: временное сопротивление 412 МПа, предел текучести 245 МПа и относительное удлинение 20-22%. Валик подъемника, подъемник замка, замкодержатель, предохранитель замка изготавливаются методом точного литья.
⟦Размеры автосцепки СА-3⟧
Все точные размеры по ГОСТ вы можете посмотреть в PDF документе.
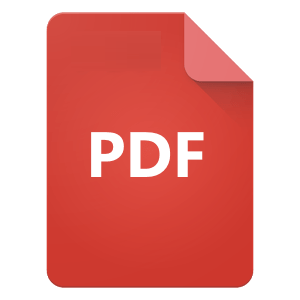
Чертеж автосцепки СА-3 с размерами:
⟦Основные неисправности⟧
В случае выявления неисправности действия механизма автосцепки, а также при единой технической ревизии пассажирских вагонов механизм автосцепки разбирают, карманы корпуса осматривают, при необходимости очищают, неисправные детали заменяют исправными и после сборки проверяют действие механизма в установленном порядке.
Не разрешается выпускать подвижной состав в эксплуатацию при наличии хотя бы одной из следующих неисправностей:
- детали автосцепного устройства с трещинами;
- разница между высотами автосцепок по обоим концам вагона более 25 мм*, провисание автосцепки подвижного состава более 10 мм; высота оси автосцепки пассажирских вагонов от головок рельсов более 1080 мм и менее 1010 мм;
- цепь или цепи расцепного привода длиной более или менее допустимой; цепь с незаваренными звеньями или надрывами в них;
- зазор между хвостовиком автосцепки и потолком ударной розетки менее 25 мм; зазор между хвостовиком и верхней кромкой окна в концевой балке менее 20 мм (при жесткой опоре хвостовика);
- замок автосцепки, отстоящий от наружной вертикальной кромки малого зуба более чем на 8 мм или менее чем на 1 мм; лапа замкодержателя, отстоящая от кромки замка менее чем на 16 мм;
- валик подъемника заедает при вращении или закреплен нетиповым способом;
- толщина перемычки хвостовика автосцепки, устанавливаемой вместо неисправной на вагон, выпускаемый из текущего отцепочного ремонта, менее 48 мм;
- поглощающий аппарат не прилегает плотно через упорную плиту к передним упорам, а также к задним упорам допускается наличие суммарного зазора между передним упором и упорной плитой или корпусом аппарата и задним упором до 5 мм;
- упорные угольники, передние и задние упоры с ослабленными заклепками;
- планка, поддерживающая тяговый хомут, толщиной менее 14 мм, либо укрепленная болтами диаметром менее 22 мм, либо без контргаек и шплинтов на болтах (допускается крепление поддерживающей планки болтами диаметром 20 мм, но в количестве 10 шт.);
- неправильно поставленные маятниковые подвески центрирующего прибора (широкими головками вниз);
- кронштейн (ограничитель вертикальных перемещений) автосцепки с трещиной в любом месте, износом горизонтальной полки или изгибом более 5 мм;
- кронштейн (ограничитель вертикальных перемещений) автосцепки с трещиной в любом месте, износом горизонтальной полки или изгибом более 5 мм;
- отсутствие предохранительного крюка у паровозной автосцепки; валик розетки, закрепленный нетиповым способом; ослабшие болты розетки; болты без шплинтов или со шплинтами, не проходящими через прорези корончатых гаек.
⟦Купить автосцепки⟧
-
Автосцепка модели СА-3 – (новая)
₽60,000
-
Автосцепка СА-3 106.01.000-0СБ (новая)
₽60,000
⟦Ремонт автосцепки СА-3⟧
Ремонт и проверка автосцепного устройства подвижного состава производятся в контрольных пунктах автосцепки (КПА) депо и отделениях по ремонту автосцепки вагоно и локомотиворемонтных заводов, а также в специализированных подразделениях предприятий по ремонту подвижного состава любой формы собственности, имеющих аттестат установленной формы, выданный железнодорожной администрацией.
Для поддержания автосцепного устройства в исправном состоянии установлены следующие виды осмотра: полный осмотр, наружний осмотр
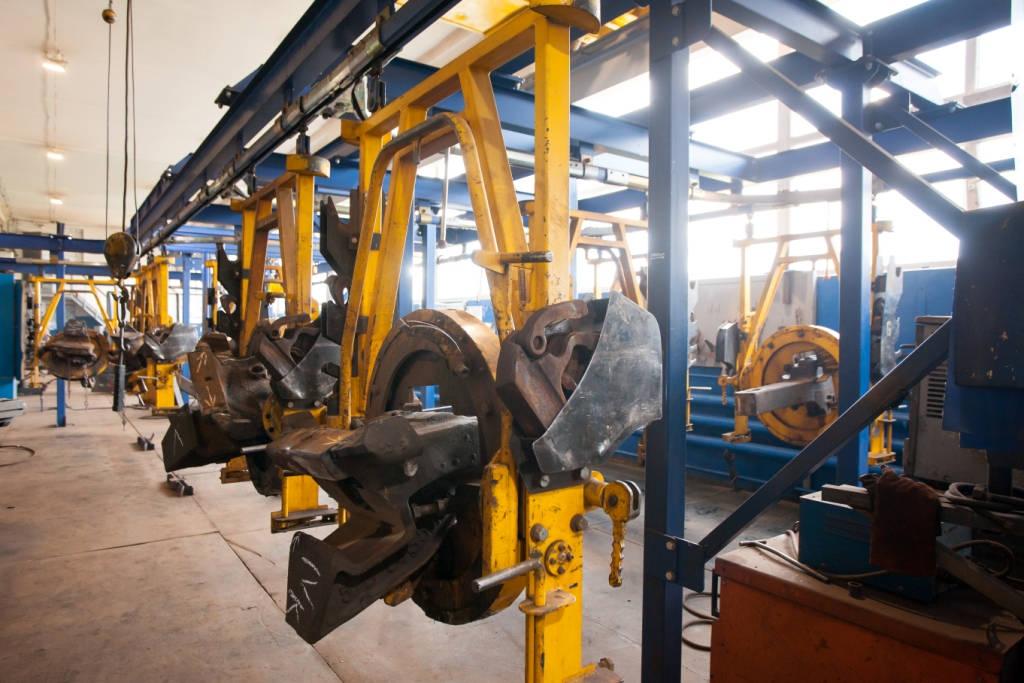
Полный осмотр автосцепного устройства производится при капитальном и деповском ремонтах вагонов, капитальном ремонте локомотивов и вагонов дизель и электропоездов, текущих ремонтах ТР-2, ТР-3 тепловозов, электровозов и вагонов дизель- и электропоездов, подъемочном ремонте паровозов и специального подвижного состава.
Наружный осмотр осуществляется при текущем отцепочном ремонте вагонов, единой технической ревизии пассажирских вагонов, промывочном ремонте паровозов, текущем ремонте ТР-1 тепловозов, электровозов и вагонов дизель и электропоездов.
⟦Прайс лист на автосцепки⟧
Если вы хотите получить прайс где можно посмотреть цены на автосцепки. То просто напишите свой Email адрес и мы пришлем вам свежие прайс листы.
⟦Варианты и развитие автосцепки СА-3⟧
С 2000-х годов на железных дорогах России применяется усовершенствованная автосцепка СА-3. При обрыве обычной автосцепки её корпус может, выскальзывая из зева сцепленной автосцепки, упасть на рельсошпальную решетку; при её падении может повредиться стрелочный перевод или, что опаснее, оказавшись на головке рельса, массивный стальной обломок может привести к крушению поезда. Усовершенствование заключается в том, что к корпусу (сверху и снизу) привариваются два кронштейна, препятствующие выскальзыванию и падению на шпалы оборванной автосцепки. В первую очередь усовершенствованные автосцепки устанавливаются на железнодорожные цистерны, предназначенные для перевозки нефтепродуктов.
В данный момент ведутся разработки стандарта автосцепки для железных дорог Европейского Союза. Конструкция одной из разработок, C-AKv (нем. Compact — Automatische Kupplung vereinfacht, компактная упрощённая автосцепка), основана на сцепке СА-3 и совместима с ней. В отличие от СА-3, в C-AKv имеется дополнительный выступ на большом зубе, который попадает в специальный паз. За счёт этого выступа сцепка работает как жёсткая, благодаря чему становится возможным автоматическое соединение электрических разъёмов и тормозных магистралей.
⟦Продажа комплектующих для автосцепки СА-3⟧
-
Аппарат поглощающий 106.02.000.2СБ – (новый)
₽47,000
-
Валик подъёмника 106.01.017-0 – (новый)
₽1,000
-
Балочка центрирующая 106.00.011-2 (новая)
₽1,800
-
Балочка центрирующая подпружиненная – (новая)
₽13,000
-
Клин тягового Хомута 106.00.002-2 (новый)
₽1,800
⟦Вопросы про автосцепку СА-3⟧
На какую силу тяги рассчитано автосцепка СА 3
Наибольшая суммарная сила тяги локомотивов, находящихся в голове поезда, при трогании поезда с места определяется исходя из максимально допустимого продольного усилия на автосцепке при трогании, равного 95 тс, а наибольшая суммарная сила тяги при разгоне и движении по труднейшему подъему определяется исходя из максимально допустимого продольного усилия на автосцепке, равного 130 тс.
⟦Видео⟧
Обновлено: 19.09.2023
ИНСТРУКЦИЯ ПО РЕМОНТУ И ОБСЛУЖИВАНИЮ АВТОСЦЕПНОГО УСТРОЙСТВА ПОДВИЖНОГО СОСТАВА ЖЕЛЕЗНЫХ ДОРОГ РОССИЙСКОЙ ФЕДЕРАЦИИ
16 сентября 1997 г.
Глава 1
1.1. Ремонт и проверка автосцепного устройства подвижного состава производятся в контрольных пунктах автосцепки (КПА) депо и отделениях по ремонту автосцепки вагоно- и локомотиворемонтных заводов, имеющих специальные удостоверения установленной формы, выдаваемые Департаментом вагонного хозяйства (ЦВ) МПС России.
1.2. Размещение технологической оснастки в пунктах ремонта автосцепного устройства должно обеспечивать выполнение требований настоящей Инструкции, а также техники безопасности и промышленной санитарии.
1.3. Контрольные пункты автосцепки депо и отделения ремонтных заводов должны иметь необходимую технологическую оснастку, два комплекта проверочных и один комплект контрольных шаблонов в соответствии с приложениями 1 и 2 настоящей Инструкции. Шаблоны должны соответствовать действующим техническим требованиям, утвержденным ЦВ МПС. Шаблоны проверяются на ремонтных предприятиях не реже одного раза в год с постановкой даты проверки согласно Методическим указаниям контроля СДК для автосцепных устройств вагонов РД 32 ЦВ-ЦЛ 027-91.
1.4. Изменение норм и допусков, указанных в настоящей Инструкции, может производиться только с разрешения ЦВ МПС. Порядок применения шаблонов в зависимости от вида ремонта подвижного состава указан в приложении 2 настоящей Инструкции.
1.5. Для поддержания автосцепного устройства в исправном состоянии установлены следующие виды осмотра: полный осмотр, наружный осмотр, проверка автосцепного устройства при техническом обслуживании подвижного состава.
1.6. Полный осмотр автосцепного устройства производится при капитальном и деповском ремонтах вагонов, капитальном ремонте локомотивов и вагонов дизель- и электропоездов, текущих ремонтах ТР-2, ТР-3 тепловозов, электровозов и вагонов дизель- и электропоездов, подъемочном ремонте паровозов. При капитальном ремонте группового рефрижераторного подвижного состава на концевых вагонах автосцепка СА-Д заменяется автосцепкой СА-3.
Наружный осмотр осуществляется при текущем отцепочном ремонте вагонов, единой технической ревизии пассажирских вагонов, промывочном ремонте паровозов, текущем ремонте ТР-1 тепловозов, электровозов и вагонов дизель- и электропоездов.
Проверяют автосцепное устройство при техническом обслуживании во время осмотра вагонов в составах на пунктах технического обслуживания (ПТО), при подготовке вагонов под погрузку и при техническом обслуживании локомотивов ТО-2, ТО-3, а также в других случаях, специально установленных МПС.
1.7. При полном осмотре съемные узлы и детали автосцепного устройства снимают с подвижного состава независимо от их состояния (кроме случаев, указанных в п.2.2.7 и 2.2.20 настоящей Инструкции) и направляют в КПА или отделение по ремонту автосцепки завода для проверки и ремонта в соответствии с требованиями, изложенными в главе 2 настоящей Инструкции. К несъемным деталям автосцепного устройства относятся: ударная розетка, передние и задние упоры, располагающиеся на хребтовой балке, детали расцепного привода (фиксирующий кронштейн, кронштейн и расцепной рычаг). Ремонт и проверку несъемных деталей производят на подвижном составе, за исключением случаев, требующих их демонтажа.
1.8. При наружном осмотре, а также при проверке автосцепного устройства во время технического обслуживания производится освидетельствование узлов и деталей в соответствии с требованиями, изложенными в главах 3 и 4 настоящей Инструкции, без снятия с подвижного состава. Снимают только неисправные узлы и детали с заменой их исправными.
1.9. Детали автосцепного устройства, снятые с подвижного состава и подлежащие проверке и ремонту, должны быть очищены от грязи средствами, имеющимися в распоряжении пункта ремонта. После очистки корпус автосцепки, тяговый хомут, клин (валик) тягового хомута, маятниковые подвески центрирующего прибора, болты паровозной розетки должны быть подвергнуты неразрушающему контролю. Стяжной болт поглощающего аппарата, опорную пластину поглощающих аппаратов ПМК-110А и ПМК-110К-23 подвергают неразрушающему контролю только после их ремонта сваркой.
1.10. Неразрушающий контроль производится в соответствии с Технологической инструкцией по испытанию на растяжение и неразрушающему контролю деталей вагонов.
1.11. Детали с дефектами, указанными в приложении 3, или не имеющие маркировки предприятия-изготовителя, ремонту не подлежат и сдаются в металлолом. При этом на каждый утилизированный корпус автосцепки составляется акт.
1.12. Все сварочные и наплавочные работы при ремонте автосцепного устройства выполняются в соответствии с требованиями Инструкции по сварке и наплавке при ремонте вагонов и контейнеров РТМ 32 ЦВ-201-88.
1.13. Слесарные, станочные работы и правка изогнутых деталей выполняются в соответствии с действующими техническими условиями МПС на производство этих работ и с требованиями Типовых технологических карт для ремонта автосцепного устройства, утвержденных МПС.
1.14. Соблюдение действующих нормативно-технических требований по ремонту автосцепного устройства проверяют руководители вагонной, пассажирской и локомотивной служб, начальники отделов вагонного, локомотивного хозяйств и пассажирских перевозок отделений, начальники вагонного (локомотивного) депо или их заместители в соответствии с личными нормативами, а на ремонтных заводах — главный инженер и начальник отдела технического контроля (ОТК) с записью в журнале ремонта.
Глава 2
Требования, указанные в настоящей главе, относятся к осмотру, проверке и ремонту автосцепного устройства при капитальном и деповском ремонтах вагонов, капитальном и текущих ремонтах ТР-2, ТР-3 тепловозов, электровозов и вагонов дизель- и электропоездов, подъемочном ремонте паровозов.
2.1. АВТОСЦЕПКА
Корпус автосцепки
2.1.1. Ширину зева корпуса автосцепки проверяют непроходным шаблоном 821р-1 по всей высоте носка большого зуба. Шаблон прикладывают одним концом к углу малого зуба (рис.2.1), а другим подводят к носку большого зуба. Если кромка шаблона пройдет мимо носка большого зуба, то зев расширен и подлежит исправлению.
Рис.2.1. Проверка ширины зева корпуса автосцепки шаблоном 821р-1:
I — корпус годен; II — корпус негоден
2.1.2. Длину малого зуба (рис.2.2, а) корпуса и расстояние между ударной стенкой зева и тяговой поверхностью большого зуба (рис.2.2, б) проверяют шаблонами 892р, 893р и 884р в зависимости от видов ремонта подвижного состава (приложение 2). Проверку выполняют в средней части по высоте зубьев на расстоянии 80 мм вверх и вниз от продольной оси корпуса. При этом зону тяговой поверхности большого зуба, находящуюся напротив окна для лапы замкодержателя, не проверяют, так как ударная стенка зева имеет литейный уклон.
Рис.2.2. Проверка шаблонами 892р, 893р, 884р:
а — длины малого зуба; б — расстояния между ударной стенкой зева и тяговой поверхностью большого зуба; I — корпус годен; II — корпус негоден (внутренняя грань 1 шаблона должна быть параллельна боковой поверхности 2 большого зуба)
Если ударная стенка зева была наплавлена и обработана, то расстояние от тяговой поверхности большого зуба до ударной стенки зева должно быть проверено и в этой зоне шаблоном 884р.
2.1.3. Контур зацепления корпуса контролируют проходным шаблоном 827р (рис.2.3), который перемещают в контуре зацепления по всей высоте так, чтобы направляющая труба 1 шаблона располагалась по закруглению в месте перехода малого зуба в ударную стенку 2 зева, а плоская часть проходила через зев и охватывала малый зуб. Контур годен, если шаблон свободно проходит через него по всей высоте головы корпуса.
Рис.2.3. Проверка контура зацепления корпуса автосцепки проходным шаблоном 827р
2.1.4. Если поверхности контура зацепления корпуса автосцепки или одна из них не соответствуют требованиям проверки шаблонами 892р, 893р или 827р, автосцепка должна быть отремонтирована с доведением до альбомных размеров соответственно шаблону 914р-м с профильной планкой 914/24-1м и непроходным щупом 914р/21а, проходным шаблонам 914р/22-м и 914р/25, непроходному 884р и проходному 827р шаблонам, шаблону 822р.
2.1.5. Шаблоном 914р-м проверяют ударную поверхность малого зуба и ударную стенку зева. Шаблон устанавливают в корпусе так, чтобы упоры а) были прижаты к ударной стенке зева, а нижняя часть и основания шаблона к внутренней стенке малого зуба.
Рис.2.4. Проверка ударных поверхностей зева и малого зуба автосцепки профильной планкой 914р/24-1м шаблона 914р-м
После установки шаблона проверяют состояние ударных поверхностей контура с помощью профильной планки 914р/24-1м и непроходного щупа 914р/21а (рис.2.4, г).
Профили рабочих поверхностей ребер планки соответствуют вертикальным профилям ударных поверхностей стенок зева и малого зуба.
Ребром 1 профильной планки 3 с надписью «Зев» проверяют ударную поверхность стенки зева, а ребром 2 с надписью «Малый зуб» — ударную поверхность малого зуба.
Для проверки ударной поверхности профильную планку прикладывают к контурным листам шаблона так, чтобы плоскость планки была перпендикулярна к проверяемой поверхности. Затем планку перемещают по кромкам контурных листов, как по копирам, по всей ширине проверяемой поверхности, а пластинку щупа вводят в зазор между ребром профильной планки и проверяемой поверхностью контура зацепления.
Если профильная планка 3 прилегает одновременно к верхнему 4 и нижнему 5 контурным листам (рис.2.4, б), то проверяемая поверхность годна. Проверяемая поверхность будет негодна (рис.2.4, в), если профильная планка прилегает плотно к нижнему 5 контурному листу, но не прилегает к верхнему 4 контурному листу или наоборот.
Проверяемая поверхность автосцепки годна (рис.2.4, г, поз.I), если щуп 6 не проходит между профильной планкой и ударной поверхностью малого зуба.
Корпус автосцепки бракуют, если непроходной щуп по всей своей ширине проходит до упора в прилив рукоятки в зазор между профильной планкой, плотно прижатой по концам к контурным листам шаблона, и проверяемой поверхностью (поз.II).
Разность зазоров между профильной планкой и ударными поверхностями малого зуба и зева вверху и внизу не должна превышать 2 мм.
Зазор между профильной планкой и ударной стенкой зева в зоне, лежащей ниже носка большого зуба, не контролируется.
2.1.6. Шаблонами 914р/22-м и 914р/25 проверяют тяговые поверхности малого и большого зубьев корпуса. При этом шаблон 914р/22-м должен свободно надеваться на малый зуб до упора в его боковую поверхность (рис.2.5, а), а шаблон 914р/25 — свободно проходить между ударной стенкой зева и тяговой поверхностью большого зуба в зоне 3 до упора ограничителей (рис.2.5, б) в боковую поверхность этого зуба, при этом выступ 1 шаблона должен опираться на кромку большого зуба 2.
Рис.2.5. Проверка малого зуба проходным шаблоном 914р/22-м (а) и тяговой поверхности большого зуба шаблоном 914р/25 (б)
2.1.7. Если при проверке корпуса установлено, что профильная планка своими концами прилегает к контурным поверхностям шаблона неплотно, или проходной шаблон для малого зуба полностью на него не находит, или проходной шаблон для большого зуба не проходит до упора в его боковую поверхность, значит на проверяемых поверхностях имеется лишний металл, который необходимо снять до плотного прилегания профильной планки к контурным поверхностям или до свободного прохода проходных шаблонов на малый и большой зубья.
Если необходимо наплавить ударные поверхности зева и малого зуба корпуса автосцепки, то толщину наплавляемого слоя определяют по зазорам и
Рис.2.6. Зазоры для определения толщины слоя наплавки поверхностей по контуру зацепления корпуса автосцепки
Для определения наибольшей допускаемой толщины наплавки тяговой поверхности малого зуба нужно из значения зазора в между ребром шаблона 914р/22-м, плотно прижатого к ударной поверхности малого зуба, и тяговой поверхностью вычесть значение ранее определенного с помощью шаблона 914р-м зазора .
Для определения толщины слоя наплавки тяговой поверхности большого зуба надо из значения зазора г между ребром шаблона 914р/25, плотно прижатого к ударной поверхности зева, и тяговой поверхностью вычесть значение ранее определенного с помощью шаблона 914р-м зазора .
2.1.8. После ремонта поверхности контура зацепления корпуса должны быть параллельны кромкам шаблона 827р.
2.1.9. Углы зева и малого зуба корпуса проверяют шаблоном 822р (рис.2.7).
Рис.2.7. Проверка закруглений углов зева 1 и малого зуба 2 шаблоном 822р:
I — угол зева годен; II — угол зева негоден; I — угол малого зуба годен; II — угол малого зуба негоден
2.1.10. При ремонте поверхностей контура зацепления корпуса не разрешается накладывать сварные швы ближе 15 мм к местам закруглений (рис.2.8, а). Переход от наплавленной ударной поверхности стенки зева к неизнашиваемой должен быть плавным на длине не менее 15 мм для беспрепятственного скольжения автосцепок друг по другу в момент сцепления. Кромка угла, образуемого наплавленной ударной поверхностью малого зуба и поверхностью, к которой прилегает замок, должна быть без закруглений по всей высоте (рис.2.8, б). Твердость наплавляемого металла ударно-тяговых поверхностей для грузовых вагонов и локомотивов должна быть не менее НВ 250, для рефрижераторных и пассажирских вагонов и вагонов электропоездов — не менее НВ 450.
Рис.2.8. Требования к поверхностям контура зацепления корпуса автосцепки после их наплавки
2.1.11. Ширина кармана для замка в корпусе считается увеличенной, если при вращении валика подъемника подъемник замка проходит мимо нижнего плеча предохранителя, не задевая его своим верхним широким пальцем. В этом случае соосно с малым отверстием для валика подъемника должна быть приварена шайба такой толщины, чтобы ширина исправленного кармана отвечала требованиям проверки непроходным шаблоном 845р и проходным 848р.
Для проверки шаблон 845р вводят в карман корпуса автосцепки через большое отверстие для валика подъемника до упора во внутреннюю стенку кармана так, чтобы шаблон касался стенки корпуса всей торцовой поверхностью (рис.2.9, а). При этом цилиндрическая часть шаблона не должна проходить между стенками кармана. Шаблон 848р вводят внутрь головы корпуса через окно для замка и пропускают между стенками кармана. Ширина кармана признается правильной, если мерительная полоса шаблона свободно проходит между стенками по всей ширине кармана (рис.2.9, б).
Рис.2.9. Проверка ширины кармана корпуса автосцепки:
а — непроходным шаблоном 845р; б — проходным шаблоном 848р; I — корпус годен; II — корпус негоден
Перед ремонтом автосцепного устройства производится его очистка от грязи. После очистки автосцепку разбирают. Детали подлежащие неразрушающему контролю подаются на позицию неразрушающего контроля. Неразрушающий контроль автосцепного устройства производится в соответствии с требованиями:
Детали автосцепного устройства подвергаемые неразрушающему контролю, а также применяемые методы, приведены в таблице 2.
Таблица 2 – Детали автосцепного устройства подвергаемые НК
МПК (хвостовик и переход от хвостовика к головной части; все зоны в головной части –только для подтверждения результатов ВТК); ВТК (все зоны в головной части)
Согласно Инструкции по ремонту и обслуживанию автосцепного устройства подвижного состава железных дорог
Плановые виды ремонта
Трещины не допускаются.
(Инструкции по ремонту и обслуживанию автосцепного устройства подвижного состава железных дорог)
Детали перед сваркой и наплавкой должны быть сухими, очищены от окалины, продуктов коррозии, краски, грязи, масла. Очистка производится механизированным способом с применением армированных абразивных кругов, стальных щеток, зубило.
Разделку трещин допускается производить: механическим способом, электродуговым или специальными электродами и поверхностно-кислородной резкой. Для электродов типа ЭЧ2 диаметром 5 мм, сила тока при разделке трещин I = 350-380А ГОСТ-9467-75.
Кромки деталей после кислородной резки должны быть зачищены от шлака, натеков и капель. Разделка трещин выполняется на всю глубину залегания до основного металла и на 15-20 мм далее видимых границ начала и конца трещины.
После разделки трещин производится зачистка основного металла на ремонтируемом участке до металлического блеска на расстоянии не менее 20мм по обе стороны от границ разделанных кромок.
Разделанные трещины в корпусе автосцепки фиксируются в специальном журнале.
При ремонте деталей автосцепного устройства сваркой и наплавкой выполняются следующий работы:
Корпус автосцепки.
Рисунок 70 – Дефекты корпуса автосцепки, устраняемые сваркой и наплавкой
При всех видах ремонта разрешается:
а) заварка вертикальных трещин в зеве сверху и снизу в углах большого зуба, деф. 6, при условии, что после разделки они не переходят на горизонтальные плоскости наружных ребер;
б) заварка трещин в углах окна для замка и замкодержателя деф. 14, при условии, что после разделки они не выходят:
— в верхних углах окна для замка — на горизонтальную стенку поверхности головки;
— в верхнем углу окна для замкодержателя — за верхнее ребро со стороны большого зуба.
В нижних углах окна для замка и замкодержателя длина этих трещин не должна превышать 20 мм.
Заварку трещин производить с местным предварительным подогревом до температуры 250 – 300°С;
в) заварка трещины перемычки между отверстием для сигнального отростка и отверстием направляющего зуба замка, если такая трещина не выходит на вертикальную стенку кармана;
г) заварка трещины в месте перехода от головной части к хвостовой, деф. 4, при условии, что после ее разделки поперечное сечение стенок не уменьшается более, чем на 25%.
д) заварка трещин перемычки, деф. 16, для автосцепок типа СА-3 и СА-3М;
е) наплавка изношенной поверхности полочки для верхнего плеча предохранителя, деф. 21;
ж) приварка отломанной полочки для верхнего плеча предохранителя.
Допускается приварка новой полочки, изготовленной из стали Ст3, в соответствии с размерами, указанными на чертежах корпуса автосцепки типа СА-3 или СА-3М.
Полочка перед приваркой должна устанавливаться в проектное положение при помощи специального кондуктора. Сварка должна производиться с полным проваром по всей толщине полочки;
и) заварка трещин, распространяющихся от отверстия для сигнального отростка, деф. 20, длиной не более 30 мм по технологии согласованной Комиссией Совета;
к) наплавка изношенной торцевой поверхности хвостовика, деф. 1, если длина хвостовика менее 645 мм для автосцепок, СА-3 и менее 654 мм — для автосцепки СА-3М. После наплавки длина хвостовика должна быть не менее 650 мм для автосцепки СА-3 и 657 мм — для СА-М;
л) наплавка изношенных поверхностей хвостовика, деф. 2, и деф. 3, при глубине износа более 3 мм;
м) наплавка изношенной поверхности в окне для замка, деф. 18, и поверхности задней наклонной части кармана в месте опоры замка, деф. 5, при износе не свыше 6 мм;
н) наплавка изношенных тяговых поверхностей малого, деф. 11, и большого зуба, деф. 7, а также ударной поверхности малого зуба, деф. 10, и зева, деф. 8, при условии, что износостойкость нанесенного слоя металла или твердость наплавленного металла при устранении дефектов 7, 10 и 11, должна быть не менее 250 НВ для грузовых и не менее 450 НВ — для рефрижераторных вагонов.
При наплавке ударной поверхности малого зуба, деф. 10, кромку угла не скруглять;
п) наплавка изношенных стенок отверстий для валика подъемника, деф. 12;
р) наплавка изношенной цилиндрической поверхности и торца шипа для замкодержателя, деф. 9, или его приварка в случае излома;
с) наплавка изношенной поверхности места опоры шейки замкодержателя, деф. 17;
т) наплавка изношенных более 3 мм но не более 8 мм стенок овального отверстия под клин, деф. 15. Перед наплавкой задней стенки данного отверстия толщина перемычки хвостовика должна быть не менее 40 мм для автосцепок СА-3 и 44 мм — для СА-3М, измеренная в средней части.
Наплавку производить после удаления дефектов в ранее наплавленном металле механической обработкой и устранения деф. 1;
у) приварка шайбы в кармане корпуса со стороны меньшего отверстия для валика подъемника в случае уширения кармана;
ф) заварка трещины ограничителя вертикального перемещения, деф. 19, или его приварка взамен погнутого или отломанного;
х) наплавка деформированной поверхности затылочной ударной части, деф. 13;
ц) заварка мелких сетчатых трещин глубиной не более 8 мм на перемычке хвостовика при условии, что после их вырубки толщина перемычки автосцепки СА-3 будет не менее 40 мм, для СА-3М – не менее 44 мм;
ч) заварка мелких сетчатых трещин на боковых поверхностях отверстия под валик или клин тягового хомута глубиной не более 8 мм при условии, что после разделки толщина оставшейся стенки автосцепки СА-3 не менее 34 мм, СА-3М — не менее 28 мм.
Замок.
При всех видах ремонта разрешается:
а) наплавка изношенной замыкающей поверхности, деф. 1, при условии, что износостойкость или твердость наплавленного (нанесенного) слоя металла не менее 250 НВ для грузовых вагонов и не менее 400 НВ — для рефрижераторных вагонов;
б) наплавка изношенной задней стенки овального отверстия для валика подъемника, деф. 3, при износе не более 8 мм;
в) приварка сигнального отростка, деф. 4;
Рисунок 71 – Дефекты замка
г) наплавка изношенных мест нижней торцевой части замка и направляющего зуба, деф. 5, 6;
д) наплавка изношенных поверхностей шипа, деф. 7, или приварка нового шипа взамен отломанного;
е) заварка отверстий в замке и вставке автосцепки типа СА-3 (рефрижераторная — для секций ЦБ-5) и СА-3М, если диаметр их в замке более 17 мм, а во вставке — более 17,5 мм;
ж) наплавка изношенной замыкающей части вставки (СА-3М) в случае несоответствия ее шаблону.
Замкодержатель.
При всех видах ремонта разрешается:
а) наплавка изношенной упорной поверхности противовеса, деф. 1;
б) наплавка изношенных стенок овального отверстия, деф. 2;
в) заварка не более одной трещины, деф. 3;
г) наплавка изношенной опорной части и торцов лапы, деф. 4;
д) наплавка изношенных поверхностей расцепного угла, деф. 5.
Рисунок 72 – Дефекты замкодержателя
Перед ремонтом автосцепного устройства производится его очистка от грязи. После очистки автосцепку разбирают. Детали подлежащие неразрушающему контролю подаются на позицию неразрушающего контроля. Неразрушающий контроль автосцепного устройства производится в соответствии с требованиями:
Детали автосцепного устройства подвергаемые неразрушающему контролю, а также применяемые методы, приведены в таблице 2.
Таблица 2 – Детали автосцепного устройства подвергаемые НК
МПК (хвостовик и переход от хвостовика к головной части; все зоны в головной части –только для подтверждения результатов ВТК); ВТК (все зоны в головной части)
Согласно Инструкции по ремонту и обслуживанию автосцепного устройства подвижного состава железных дорог
Плановые виды ремонта
Трещины не допускаются.
(Инструкции по ремонту и обслуживанию автосцепного устройства подвижного состава железных дорог)
Детали перед сваркой и наплавкой должны быть сухими, очищены от окалины, продуктов коррозии, краски, грязи, масла. Очистка производится механизированным способом с применением армированных абразивных кругов, стальных щеток, зубило.
Разделку трещин допускается производить: механическим способом, электродуговым или специальными электродами и поверхностно-кислородной резкой. Для электродов типа ЭЧ2 диаметром 5 мм, сила тока при разделке трещин I = 350-380А ГОСТ-9467-75.
Кромки деталей после кислородной резки должны быть зачищены от шлака, натеков и капель. Разделка трещин выполняется на всю глубину залегания до основного металла и на 15-20 мм далее видимых границ начала и конца трещины.
После разделки трещин производится зачистка основного металла на ремонтируемом участке до металлического блеска на расстоянии не менее 20мм по обе стороны от границ разделанных кромок.
Разделанные трещины в корпусе автосцепки фиксируются в специальном журнале.
При ремонте деталей автосцепного устройства сваркой и наплавкой выполняются следующий работы:
Корпус автосцепки.
Рисунок 70 – Дефекты корпуса автосцепки, устраняемые сваркой и наплавкой
При всех видах ремонта разрешается:
а) заварка вертикальных трещин в зеве сверху и снизу в углах большого зуба, деф. 6, при условии, что после разделки они не переходят на горизонтальные плоскости наружных ребер;
б) заварка трещин в углах окна для замка и замкодержателя деф. 14, при условии, что после разделки они не выходят:
— в верхних углах окна для замка — на горизонтальную стенку поверхности головки;
— в верхнем углу окна для замкодержателя — за верхнее ребро со стороны большого зуба.
В нижних углах окна для замка и замкодержателя длина этих трещин не должна превышать 20 мм.
Заварку трещин производить с местным предварительным подогревом до температуры 250 – 300°С;
в) заварка трещины перемычки между отверстием для сигнального отростка и отверстием направляющего зуба замка, если такая трещина не выходит на вертикальную стенку кармана;
г) заварка трещины в месте перехода от головной части к хвостовой, деф. 4, при условии, что после ее разделки поперечное сечение стенок не уменьшается более, чем на 25%.
д) заварка трещин перемычки, деф. 16, для автосцепок типа СА-3 и СА-3М;
е) наплавка изношенной поверхности полочки для верхнего плеча предохранителя, деф. 21;
ж) приварка отломанной полочки для верхнего плеча предохранителя.
Допускается приварка новой полочки, изготовленной из стали Ст3, в соответствии с размерами, указанными на чертежах корпуса автосцепки типа СА-3 или СА-3М.
Полочка перед приваркой должна устанавливаться в проектное положение при помощи специального кондуктора. Сварка должна производиться с полным проваром по всей толщине полочки;
и) заварка трещин, распространяющихся от отверстия для сигнального отростка, деф. 20, длиной не более 30 мм по технологии согласованной Комиссией Совета;
к) наплавка изношенной торцевой поверхности хвостовика, деф. 1, если длина хвостовика менее 645 мм для автосцепок, СА-3 и менее 654 мм — для автосцепки СА-3М. После наплавки длина хвостовика должна быть не менее 650 мм для автосцепки СА-3 и 657 мм — для СА-М;
л) наплавка изношенных поверхностей хвостовика, деф. 2, и деф. 3, при глубине износа более 3 мм;
м) наплавка изношенной поверхности в окне для замка, деф. 18, и поверхности задней наклонной части кармана в месте опоры замка, деф. 5, при износе не свыше 6 мм;
н) наплавка изношенных тяговых поверхностей малого, деф. 11, и большого зуба, деф. 7, а также ударной поверхности малого зуба, деф. 10, и зева, деф. 8, при условии, что износостойкость нанесенного слоя металла или твердость наплавленного металла при устранении дефектов 7, 10 и 11, должна быть не менее 250 НВ для грузовых и не менее 450 НВ — для рефрижераторных вагонов.
При наплавке ударной поверхности малого зуба, деф. 10, кромку угла не скруглять;
п) наплавка изношенных стенок отверстий для валика подъемника, деф. 12;
р) наплавка изношенной цилиндрической поверхности и торца шипа для замкодержателя, деф. 9, или его приварка в случае излома;
с) наплавка изношенной поверхности места опоры шейки замкодержателя, деф. 17;
т) наплавка изношенных более 3 мм но не более 8 мм стенок овального отверстия под клин, деф. 15. Перед наплавкой задней стенки данного отверстия толщина перемычки хвостовика должна быть не менее 40 мм для автосцепок СА-3 и 44 мм — для СА-3М, измеренная в средней части.
Наплавку производить после удаления дефектов в ранее наплавленном металле механической обработкой и устранения деф. 1;
у) приварка шайбы в кармане корпуса со стороны меньшего отверстия для валика подъемника в случае уширения кармана;
ф) заварка трещины ограничителя вертикального перемещения, деф. 19, или его приварка взамен погнутого или отломанного;
х) наплавка деформированной поверхности затылочной ударной части, деф. 13;
ц) заварка мелких сетчатых трещин глубиной не более 8 мм на перемычке хвостовика при условии, что после их вырубки толщина перемычки автосцепки СА-3 будет не менее 40 мм, для СА-3М – не менее 44 мм;
ч) заварка мелких сетчатых трещин на боковых поверхностях отверстия под валик или клин тягового хомута глубиной не более 8 мм при условии, что после разделки толщина оставшейся стенки автосцепки СА-3 не менее 34 мм, СА-3М — не менее 28 мм.
Замок.
При всех видах ремонта разрешается:
а) наплавка изношенной замыкающей поверхности, деф. 1, при условии, что износостойкость или твердость наплавленного (нанесенного) слоя металла не менее 250 НВ для грузовых вагонов и не менее 400 НВ — для рефрижераторных вагонов;
б) наплавка изношенной задней стенки овального отверстия для валика подъемника, деф. 3, при износе не более 8 мм;
в) приварка сигнального отростка, деф. 4;
Рисунок 71 – Дефекты замка
г) наплавка изношенных мест нижней торцевой части замка и направляющего зуба, деф. 5, 6;
д) наплавка изношенных поверхностей шипа, деф. 7, или приварка нового шипа взамен отломанного;
е) заварка отверстий в замке и вставке автосцепки типа СА-3 (рефрижераторная — для секций ЦБ-5) и СА-3М, если диаметр их в замке более 17 мм, а во вставке — более 17,5 мм;
ж) наплавка изношенной замыкающей части вставки (СА-3М) в случае несоответствия ее шаблону.
Детали автосцепного устройства изнашиваются в результате воздействия ударных и тяговых нагрузок.
В процессе работы на автосцепку действует тяговое усилие Τ1 (рис. 150, а). Составляющие его: R1 — приложено к большому зубу, — к малому зубу и R3 — к замку. Возникающие при этом силы трения: μR1 и μR2 действуют в плоскостях соприкосновения зубьев и μR3 — в плоскости соприкосновения замков, где μ — коэффициент трения. Усилия R1 и R2 равны примерно 0,45 Τ1, а R3≈ 0,32Т1.
Рис. 150. Схема сил, действующих в контуре зацепления автосцепки
Наибольшее тяговое усилие Τ1, действующее на грузовой вагон при трогании с места без ударов, равно примерно 250 т. При неблагоприятных условиях продольной динамики поезда это усилие возрастает и в элементах рамы могут возникать напряжения, превосходящие допустимые.
При сжатии двух автосцепок силой Т2 (рис. 150, б) в ударных поверхностях контура зацепления возникают нормальные усилия R1, R2 и R3, а также силы трения
Ввиду сложности очертания корпуса автосцепки и непостоянства положения точек приложения сил трения возможна скорее качественная, чем количественная оценка их действия.
Указанные выше усилия, действующие в контуре зацепления, вызывают в сечениях 1 — 6 (рис. 150, в) напряженное состояние, а силы трения как при растяжении, так и при сжатии,— износ поверхностей контура зацепления корпуса автосцепки и опорной части хвостовика.
На величину износа большое влияние оказывают динамические усилия, которые, так же как и силы трения, переменны. Износ тем больше, чем больше величины действующих статических и динамических усилий, чем больше относительная скорость перемещения автосцепок. Величина износа также зависит от состояния пути, подвижного состава, от допусков на зазоры между контурами зацепления двух автосцепок и т. п.
Для своевременного выявления износа и повреждений деталей автосцепки и их устранения в эксплуатации и при текущем отцепочном ремонте вагонов (независимо от причины отцепки вагона в ремонт) производится наружный осмотр автосцепного устройства, а при всех периодических ремонтах — полный осмотр с обязательным снятием с вагона и разборкой автосцепки и поглощающего аппарата.
Осмотр и ремонт автосцепки выполняются в соответствии с правилами, утвержденными МПС. Снятые с вагонов автосцепки, поглощающие аппараты и тяговые хомуты направляются в специальное отделение (контрольный пункт) для освидетельствования и ремонта. Корпус автосцепки, детали сцепного механизма и поглощающего аппарата, имеющие износ и повреждения свыше допускаемых размеров, ремонтируются или заменяются новыми.
2. Ремонт корпуса автосцепки
К основным неисправностям корпуса автосцепки относятся: износ тяговых и ударных поверхностей большого и малого зубьев, а также зева; износ упоров корпуса в месте соприкосновения с ударной розеткой, отверстия для клина и опорной части хвостовика; трещины в углах зева, окнах для замка и замкодержателя; износ полочки, шипа и некоторых других частей корпуса. Указанные износ и повреждения устраняются электродуговой сваркой или наплавкой (рис. 151). Для повышения износоустойчивости наплавки целесообразно применять легированные электроды со специальными присадками в толстой обмазке.
Рис. 151. Отремонтированный сваркой корпус автосцепки: а — вид сверху; б — вид сбоку; в — вид спереди; 1 — заваренные трещины в углах зева и окна для замка и замкодержателя; 2 — заваренные трещины в хвостовике; 3 — приваренная полочка; 4 — наплавленная поверхность контура зацепления; 5 — наплавленная перемычка хвостовика; 6 — наплавленные поверхности хвостовика; 7 — наплавленная нижняя перемычка в окне для замка; 8 — заваренная протертость шейки уха; 9 — наплавленный буртик уха; 10 — наплавленное отверстие для валика подъемника; 11 — наплавленная передняя поверхность полочки; 12 — наплавленный шип для замкодержателя
Сравнительная оценка износоустойчивости наплавленного слоя в зависимости от вида присадки, включенной в толстую обмазку, показывает, что наиболее благоприятное влияние на износоустойчивость стали оказывает марганец (Мn) (рис. 152). Кроме того, в условиях работы на износ при ударах и высоких удельных давлениях Мп имеет также лучшие показатели по сравнению с Сr, W и Ni и к тому же он дешевле и менее дефицитен.
Кроме того, наплавка под слоем флюса позволяет связывать азот и кислород, находящиеся в металле, ранее наплавленном электродами с меловой обмазкой. Режим наплавки: сварочный ток 400—500 а, скорость подачи каждой электродной проволоки — 126 мм; напряжение дуги 30—36 в; скорость наплавки 12 — 15 м/ч. Наплавка производится постоянным или переменным током, причем при постоянном токе качество наплавки лучше.
Для электросварочных работ корпус автосцепки закрепляется на стенде так, чтобы наплавляемая поверхность находилась в нижнем положении. После установки автосцепки укрепляется флюсоудерживающее приспособление, и мундштуки подводятся к исходному положению. Для облегчения возбуждения дуги один из электродов закорачивается на зачищенной до металлического блеска поверхности. Вылет электродов за контактную поверхность мундштуков должен быть около 30 мм.
Рис. 154. Стенд для автоматической наплавки автосцепки и других деталей сварочным аппаратом ΠШ-5-Ж
Электроды располагаются гребенкой по ширине наплавляемого участка с расстоянием между осями 7 — 8 мм. Это позволяет наплавлять за один проход тремя электродами валик шириной 35 — 40 мм. Перед наплавкой второго слоя необходимо удалить шлаковую корку с первого валика· и установить электроды так, чтобы они перекрывали предыдущий валик на 4 — 5 мм.
Широкое применение полуавтоматов ПШ-5 и ПШ-54 значительно расширило технологические возможности сварки под слоем флюса. Сварка может производиться в нижнем и наклонном положениях. Вместе с этим шланговая полуавтоматическая сварка имеет некоторые недостатки, в частности затруднено ведение электрода вручную вдоль линии наплавки, так как место сварки закрыто флюсом; производительность наплавки ниже, чем при автоматической сварке.
В вагонных депо Юго-Западной дороги ручное перемещение электрододержателя полуавтоматов ПШ-5 и ПШ-54 заменено механизированным, что позволило повысить производительность и улучшить качество сварочных работ. Так, в вагонном депо станции Жмеринка Юго-Западной дороги изготовлен стенд (рис. 151) для автоматической наплавки сварочным аппаратом ПШ-5-Ж изношенных поверхностей корпуса автосцепки и других деталей. Этот стенд значительно расширяет возможности механизации наплавочных работ и позволяет устанавливать корпус автосцепки в любое положение для наплавки тяговой поверхности большого и малого зубьев, ударной поверхности малого зуба и зева, боковой поверхности и перемычки хвостовика. Стенд состоит из колонны 1, изготовленной из двутавровой балки № 25 длиной 2 315 мм. По неподвижной рейке 6 на колонне с помощью зубчатого колеса 18, роликов 5 и упорных роликов 17 перекатывается каретка 12. Перемещение последней осуществляется вращением рукоятки 13 при незначительном усилии, так как каретка вместе с закрепленной в ней автосцепкой уравновешивается противовесом 4 (240 кг), который подвешен на тросе 3 с противоположной стороны каретки и кондуктора. Трос соединяется с кареткой через ролик 2, укрепленный на вершине колонны 1. В каретке укреплен кондуктор, состоящий из вращающегося патрона 11, который установлен на двух шарикоподшипниках. К патрону приварен кронштейн 19 с круглой розеткой 10, вращающейся на роликах 20. К розетке 10 приварена опорная плита 9 для прикрепления автосцепки. Эта плита вращается вместе с розеткой.
Рис. 155. Поверхности контура зацепления корпуса автосцепки, восстановленные сваркой
Автосцепка, установленная в кондукторе, прикрепляется к опорной плите скобами 8 и хомутом 7. Кондуктор соприкасается с двух направляющих колонной только с одной стороны, в результате чего наплавляемая автосцепка доступна сварщику со всех сторон.
Для установки автосцепки на стенде в требуемое положение имеются три фиксатора: каретка 14, патрон 15 и розетка 16. Постановка и снятие автосцепки осуществляются воздушным подъемником. Наплавка производится под слоем флюса, который поступает из бункера 21 по гибкому шлангу в зону наплавки.
На тяговых поверхностях большого и малого зубьев первый валик наплавляется на расстоянии 15 мм от закругления, т. е. мест наибольших напряжений (рис. 155). Переход от наплавленного слоя к основному металлу должен быть плавным. Толщина наплавляемого слоя определяется с учетом припуска на механическую обработку; его объем контролируется шаблонами.
Поверхности контура зацепления автосцепки должны наплавляться и обрабатываться с большой точностью. Некачественная и неточная обработка наплавленной поверхности вызывает не только усиленный износ соприкасающейся поверхности автосцепки, но в ряде случаев приводит к нарушению работы механизма автосцепки и к саморасцепу.
При наплавке корпусов автосцепки и деталей автосцепного устройства ручным способом рекомендуется применять специальные электроды типов ЭНХ25, ЭНХ30 или Э42, Э50. К первым относятся, например, электроды МИИТа, разработанные доц. М. Г. Макеевым. В состав покрытия таких электродов входит: ферромарганец — 45%, мрамор или полевой шпат—26%, гематит— 26%, крахмал—3% и жидкое стекло, которое добавляется по весу к сухой смеси в количестве 25%. Указанные электроды могут применяться как при постоянном, так и переменном токе. Они обеспечивают устойчивое горение дуги независимо от ее длины и изменения утла наклона электрода, хорошее формирование шва, отсутствие пор в наплавленном металле, легкую отделяемость шлака, повышенную твердость наплавленного слоя, высокую производительность. Плавное повышение твердости наплавленного слоя при применении этих электродов (рис. 156) весьма ценно, так как оно характеризует хорошее сплавление основного металла с электродным и увеличивает износоустойчивость и долговечность работы автосцепки.
При больших объемах наплавочных работ, выполняемых вручную, их рационально производить пучком электродов или одиночным электродом диаметром 8 — 9 мм, значительно повышающим производительность наплавки. Кроме того, наплавка пучком электродов и одиночным с увеличенным, диаметром улучшает качество металла в зоне сплавления.
Заварка трещин в корпусе автосцепки является ответственной операцией. Эта работа должна выполняться высококвалифицированными сварщиками, имеющими право производить ответственные сварочные работы.
Рис. 156. График изменения твердости в различных участках зоны наплавки: а — зона наплавленного металла; б— зова основного металла
Рис. 157. Сжатие расширенного зева корпуса автосцепки
Выправление хвостовика производится зажатием или легкими ударами бойка молота, а сжатие зева — постепенным нагружением большого зуба автосцепки бойком молота усилием Р (рис. 157), пользуясь ограничителем сжатия а.
Рис. 158. Приспособление для обработки рабочих поверхностей контура зацепления автосцепки на строгальном станке:
а — общий вид приспособления; б —подающее устройство; в — тип резцов, применяемых при обработке; А — съемная часть; Б —несъемная часть; 1 — кронштейн несъемной части приспособления; 2 — подвижная плита; 3 — наклонные направляющие; 4 — болты для укрепления корпуса; 5 — поддерживающий болт; 6 — направляющие планки; 7 — основание съемной части; 8 — стопорные болты; 9 — клинообразные пластины; 10 — неподвижная градуированная шкала; 11 — указатель; 12 — винт для перемещения плиты; 13 — рукоятка для вращения корпуса
Рис. 159. Обработка наплавленных поверхностей перемычки хвостовика автосцепки на горизонтальнофрезерном станке:
1 — планка крепления с болтами; 2 — гайка крепления фрезы; 3 — отъемный хобот фрезерного станка; 4 — фреза для обработки перемычки хвостовика; 5 — рукоятка горизонтальной подачи стола
Для устранения внутренних напряжений корпус автосцепки после выправления вторично нагревается до той же температуры и медленно охлаждается в закрытом помещении. Сжатие зева и выправление хвостовика могут производиться только при отсутствии трещин в зоне выправляемых мест. При выполнении этих работ необходимо тщательно следить за сохранением формы и размеров зева и хвостовика с проверкой их шаблонами.
Наплавленные поверхности контура зацепления и хвостовика подвергаются механической обработке. Сложность обработки этих поверхностей заключается не только в том, чтобы выдержать установленные шаблонами расстояния между ударными и тяговыми поверхностями, но и в том, чтобы правильно выполнить ломаный (по высоте) профиль поверхностей малого и большого зубьев.
Корпус автосцепки укладывается на приспособление так, чтобы его продольная ось находилась под прямым углом к линии движения резца. Вначале прострагивается поверхность по всей длине и ширине до установленных размеров, проверяемых шаблонами. Затем слегка ослабляются крепящие болты 4 и вращением рукоятки 13 корпус автосцепки поворачивается в ту или другую сторону на необходимый угол к линии движения резца для строгания наклонных площадок на рабочих поверхностях малого и большого зубьев. Установка корпуса облегчается при пользовании неподвижной градуированной шкалой 10, по которой ведутся отсчеты в том и другом направлении.
Контур зацепления обрабатывают на строгальном станке, применяя приспособление (рис. 158) для закрепления корпуса автосцепки на столе станка под необходимым углом к линии движения резца. Съемная часть приспособления (А) постоянно закреплена на столе станка и не препятствует выполнению
Нарушение формы и размеров контура зацепления может привести к затруднениям при сцеплении или расцеплении автосцепок и даже к их саморасцепу.
После наплавки и механической обработки поверхностей контур зацепления проверяется проходным шаблоном, а вертикальный профиль ударных поверхностей зева и малого зуба — профильной планкой.
Наплавленная поверхность перемычки хвостовика автосцепки обрабатывается на вертикально- или горизонтально-фрезерном станке (рис. 159). Обработку можно производить и на токарном станке оправкой с резцом. Перемычка со стороны отверстия для клина должна обрабатываться так, чтобы получилась ровная цилиндрическая поверхность с радиусом кривизны не менее 16 и не более 20 мм с плавным переходом к боковым поверхностям стенок отверстия. После обработки перемычка проверяется специальным шаблоном, в соответствии с которым толщина ее должна быть не менее 50 мм.
Автосцепка СА-3 — это автоматическое ударно-тяговое сцепное устройство не жесткого типа, служащее для сцепления элементов подвижного состава между собой. К деталям автосцепки СА-3 относят: корпус автосцепки, замок, замкодержатель, предохранитель замка, подъемник замка, валик подъемника. Автосцепка СА-3 и унифицированные с ней детали могут иметь дополнительные устройства и конструктивные исполнения, исходя из требований к конкретной единице железнодорожного подвижного состава.
Конструкцией автосцепки модели СА-3, массово применяемой на железных дорогах более 70 лет без существенных изменений, обеспечиваются сцепление и исключение разъединения вагонов при движении поезда в случае, если перед сцеплением разница по высоте между автосцепками не превышает 100 мм. Причиной такого ограничения является необходимость обеспечить достаточную величину площадки перекрытия замков. При превышении установленной разницы сцепление будет ненадежным, и при проходе по криволинейным участкам пути может произойти саморасцеп.
⟦Устройство и назначение⟧
Автосцепное устройство представляет собой комплект сборочных единиц и деталей для автоматического сцепления единиц подвижного состава, удержания их на определенном расстоянии друг от друга, а также передачи и амортизации продольных сил. Для автосцепных устройств существует ограничение, вызванное особенностью их конструкции. Данное ограничение заключается в обеспечении автоматического сцепления вагонов только в случае не превышения определенной величины разности высот уровней осей сцепляемых автосцепок. Это ограничение позволяет учесть возможные понижения конструкции вагона после его изготовления за счет износов, прогиба рессорного подвешивания и допусков установки.
Рисунок №1
Рисунок №2
Рисунок №3
⟦Размеры автосцепки СА-3⟧
Все точные размеры по ГОСТ вы можете посмотреть в PDF документе.
ГОСТ 32885—2014
АВТОСЦЕПКА МОДЕЛИ СА-3
Конструкция и размеры
Чертеж с размерами:
⟦Основные неисправности⟧
В случае выявления неисправности действия механизма автосцепки, а также при единой технической ревизии пассажирских вагонов механизм автосцепки разбирают, карманы корпуса осматривают, при необходимости очищают, неисправные детали заменяют исправными и после сборки проверяют действие механизма в установленном порядке.
Не разрешается выпускать подвижной состав в эксплуатацию при наличии хотя бы одной из следующих неисправностей:
- детали автосцепного устройства с трещинами;
- разница между высотами автосцепок по обоим концам вагона более 25 мм*, провисание автосцепки подвижного состава более 10 мм; высота оси автосцепки пассажирских вагонов от головок рельсов более 1080 мм и менее 1010 мм;
- цепь или цепи расцепного привода длиной более или менее допустимой; цепь с незаваренными звеньями или надрывами в них;
- зазор между хвостовиком автосцепки и потолком ударной розетки менее 25 мм; зазор между хвостовиком и верхней кромкой окна в концевой балке менее 20 мм (при жесткой опоре хвостовика);
- замок автосцепки, отстоящий от наружной вертикальной кромки малого зуба более чем на 8 мм или менее чем на 1 мм; лапа замкодержателя, отстоящая от кромки замка менее чем на 16 мм;
- валик подъемника заедает при вращении или закреплен нетиповым способом;
- толщина перемычки хвостовика автосцепки, устанавливаемой вместо неисправной на вагон, выпускаемый из текущего отцепочного ремонта, менее 48 мм;
- поглощающий аппарат не прилегает плотно через упорную плиту к передним упорам, а также к задним упорам допускается наличие суммарного зазора между передним упором и упорной плитой или корпусом аппарата и задним упором до 5 мм;
- упорные угольники, передние и задние упоры с ослабленными заклепками;
- планка, поддерживающая тяговый хомут, толщиной менее 14 мм, либо укрепленная болтами диаметром менее 22 мм, либо без контргаек и шплинтов на болтах (допускается крепление поддерживающей планки болтами диаметром 20 мм, но в количестве 10 шт.);
- неправильно поставленные маятниковые подвески центрирующего прибора (широкими головками вниз);
- кронштейн (ограничитель вертикальных перемещений) автосцепки с трещиной в любом месте, износом горизонтальной полки или изгибом более 5 мм;
- кронштейн (ограничитель вертикальных перемещений) автосцепки с трещиной в любом месте, износом горизонтальной полки или изгибом более 5 мм;
- отсутствие предохранительного крюка у паровозной автосцепки; валик розетки, закрепленный нетиповым способом; ослабшие болты розетки; болты без шплинтов или со шплинтами, не проходящими через прорези корончатых гаек.
Купить автосцепки
Автосцепка модели СА-3 — (новая)
Автосцепка СА-3 106.01.000-0СБ (новая)
⟦Ремонт автосцеки СА-3⟧
Ремонт и проверка автосцепного устройства подвижного состава производятся в контрольных пунктах автосцепки (КПА) депо и отделениях по ремонту автосцепки вагоно и локомотиворемонтных заводов, а также в специализированных подразделениях предприятий по ремонту подвижного состава любой формы собственности, имеющих аттестат установленной формы, выданный железнодорожной администрацией.
Для поддержания автосцепного устройства в исправном состоянии установлены следующие виды осмотра: полный осмотр, наружный осмотр
Полный осмотр автосцепного устройства производится при капитальном и деповском ремонтах вагонов, капитальном ремонте локомотивов и вагонов дизель и электропоездов, текущих ремонтах ТР-2, ТР-3 тепловозов, электровозов и вагонов дизель- и электропоездов, подъемочном ремонте паровозов и специального подвижного состава.
Наружный осмотр осуществляется при текущем отцепочном ремонте вагонов, единой технической ревизии пассажирских вагонов, промывочном ремонте паровозов, текущем ремонте ТР-1 тепловозов, электровозов и вагонов дизель и электропоездов.
Прайс лист на автосцепки
Если вы хотите получить прайс где можно посмотреть цены на автосцепки. То просто напишите свой Email адрес и мы пришлем вам свежие прайс листы.
Варианты и развитие автосцепки СА-3
С 2000-х годов на железных дорогах России применяется усовершенствованная автосцепка СА-3. При обрыве обычной автосцепки её корпус может, выскальзывая из зева сцепленной автосцепки, упасть на рельсошпальную решетку; при её падении может повредиться стрелочный перевод или, что опаснее, оказавшись на головке рельса, массивный стальной обломок может привести к крушению поезда. Усовершенствование заключается в том, что к корпусу (сверху и снизу) привариваются два кронштейна, препятствующие выскальзыванию и падению на шпалы оборванной автосцепки. В первую очередь усовершенствованные автосцепки устанавливаются на железнодорожные цистерны, предназначенные для перевозки нефтепродуктов.
В данный момент ведутся разработки стандарта автосцепки для железных дорог Европейского Союза. Конструкция одной из разработок, C-AKv (нем. Compact — Automatische Kupplung vereinfacht, компактная упрощённая автосцепка), основана на сцепке СА-3 и совместима с ней. В отличие от СА-3, в C-AKv имеется дополнительный выступ на большом зубе, который попадает в специальный паз. За счёт этого выступа сцепка работает как жёсткая, благодаря чему становится возможным автоматическое соединение электрических разъёмов и тормозных магистралей.
Автосцепка C-AKv
Читайте также:
- Юдифь и олоферн легенда кратко
- Военные конфликты в 1990 е в рф кратко
- Каково назначение объектива и окуляра в телескопе кратко
- История открытия радиоволн кратко
- Дисциплина мать победы объяснение кратко